Three-dimensional curve stretch forming method based on multi-point force loading mode
A technology of stretch forming and three-dimensional curved surface, which is applied in the field of stretch forming and sheet metal forming of large three-dimensional curved parts, and can solve the problem that the elongation cannot be effectively controlled.
- Summary
- Abstract
- Description
- Claims
- Application Information
AI Technical Summary
Problems solved by technology
Method used
Image
Examples
specific Embodiment approach
[0064] The three-dimensional curved surface drawing and forming method based on the multi-point force loading method involved in the present invention, such as figure 1 As shown, the m left loading control units 2 arranged on the left side of the drawing die 1 and the m right loading control units 3 arranged on the right side of the drawing die 1 are used as the drawing forming loading tools, and at the left end of the sheet material On the m discrete loading control points 4 at the left end of the upper part and the m discrete loading control points 5 at the right end of the sheet metal, real-time controlled stretching force is applied to the sheet metal, such as image 3 As shown, the sheet material is gradually attached to the mold surface 6 in a deformation mode with the minimum stretching deformation elongation, and a high-quality stretch-formed curved surface part 7 is obtained, as shown in Figure 4 As shown; the m left loading control units 2 and the m right loading co...
PUM
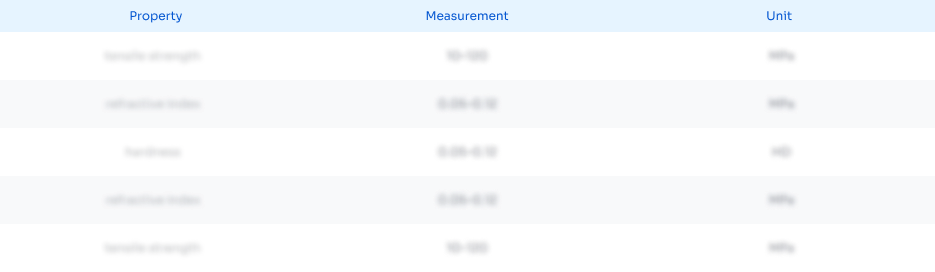
Abstract
Description
Claims
Application Information

- R&D
- Intellectual Property
- Life Sciences
- Materials
- Tech Scout
- Unparalleled Data Quality
- Higher Quality Content
- 60% Fewer Hallucinations
Browse by: Latest US Patents, China's latest patents, Technical Efficacy Thesaurus, Application Domain, Technology Topic, Popular Technical Reports.
© 2025 PatSnap. All rights reserved.Legal|Privacy policy|Modern Slavery Act Transparency Statement|Sitemap|About US| Contact US: help@patsnap.com