Assembly type hidden beam floor system
A prefabricated and floor-to-floor technology, which is applied to floors, building components, buildings, etc., can solve the problems of difficult controllability, long molding time, and affecting construction speed, etc.
- Summary
- Abstract
- Description
- Claims
- Application Information
AI Technical Summary
Problems solved by technology
Method used
Image
Examples
Embodiment Construction
[0019] The invention will be further described below in conjunction with the accompanying drawings.
[0020] figure 1It is a plan view of a prefabricated concealed beam floor of the present invention. When the present invention is implemented, the prefabricated assembled flangeless cavity plate member 7 produced in the factory assembly line is transported to the construction site; the so-called columns and beams are reinforced concrete structures or steel structure; the assembled flangeless cavity plate member and the beam can be divided into vertical lamination or horizontal lamination; the vertical lamination is the lamination of the assembled flangeless cavity plate member on the beam The top surface; the horizontal stacking is to stack the assembled flangeless cavity plate member on the horizontal plane of the beam. When the column 2 and the beam 3 are shaped steel structures, the exposed rib steel bars 4 are directly welded to the shaped steel columns and shaped steel be...
PUM
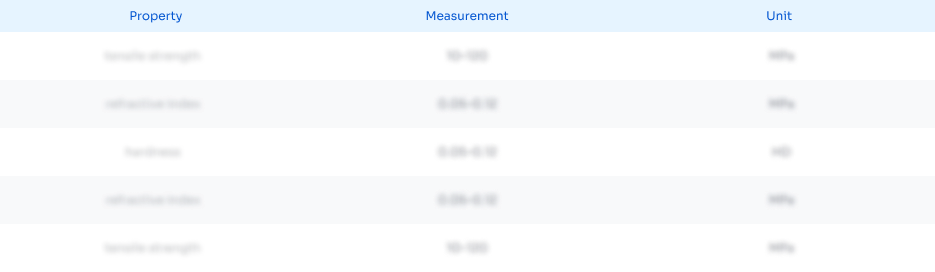
Abstract
Description
Claims
Application Information

- R&D
- Intellectual Property
- Life Sciences
- Materials
- Tech Scout
- Unparalleled Data Quality
- Higher Quality Content
- 60% Fewer Hallucinations
Browse by: Latest US Patents, China's latest patents, Technical Efficacy Thesaurus, Application Domain, Technology Topic, Popular Technical Reports.
© 2025 PatSnap. All rights reserved.Legal|Privacy policy|Modern Slavery Act Transparency Statement|Sitemap|About US| Contact US: help@patsnap.com