Tensile integrated bionic knee joint
A technology of tensegrity and knee joints, which is applied in the field of bionic knee joints, can solve the problems of joint failure, poor impact absorption ability, high energy consumption for joint stability, and achieve the effect of improving stability
- Summary
- Abstract
- Description
- Claims
- Application Information
AI Technical Summary
Problems solved by technology
Method used
Image
Examples
Embodiment Construction
[0022] see figure 1 , figure 2 , image 3 and Figure 4 As shown, this embodiment includes a first rigid compression unit 1 , a cable unit 2 and a second rigid compression unit 3 .
[0023] The first rigid compression unit 1 is composed of the first rigid compression unit main body 11, the first support rod 12, the second support rod 17, the third support rod 19, and the fourth support rod 122. Two groups of symmetrically distributed The first support rod 12 is fixedly connected to the main body 11 of the first rigid compression unit through four sets of first screws 13; On the unit main body 11; a pair of symmetrically distributed third support rods 19 are fixed between the two groups of first support rods 12 by two pairs of fifth screws 120 to enhance the overall support rigidity; four evenly distributed fourth support rods 122 are fixedly connected with the first support rod 12 through sixth screws 121 respectively.
[0024] The cable unit 2 is composed of a first bio...
PUM
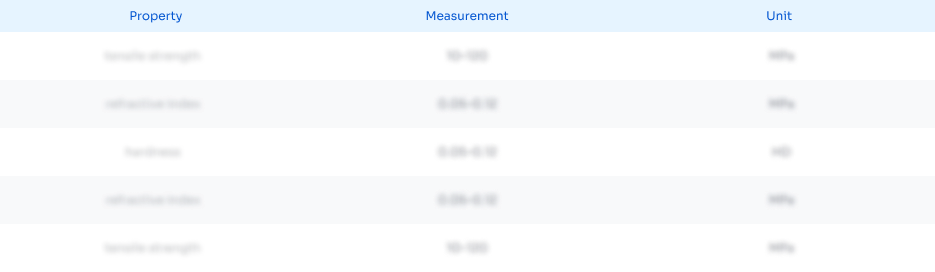
Abstract
Description
Claims
Application Information

- Generate Ideas
- Intellectual Property
- Life Sciences
- Materials
- Tech Scout
- Unparalleled Data Quality
- Higher Quality Content
- 60% Fewer Hallucinations
Browse by: Latest US Patents, China's latest patents, Technical Efficacy Thesaurus, Application Domain, Technology Topic, Popular Technical Reports.
© 2025 PatSnap. All rights reserved.Legal|Privacy policy|Modern Slavery Act Transparency Statement|Sitemap|About US| Contact US: help@patsnap.com