Embraced type sensor vibration reducing bracket with adjustable installing and pointing accuracy
A technology of pointing accuracy and sensors, applied in aerospace vehicles, aircraft, transportation and packaging, etc., can solve problems such as non-structural design, achieve simple structure, high support reliability, and improve the effect of mechanical environment
- Summary
- Abstract
- Description
- Claims
- Application Information
AI Technical Summary
Problems solved by technology
Method used
Image
Examples
Embodiment Construction
[0015] See attached figure 1 : Surrounding type adjustable installation pointing accuracy sensor vibration damping support, which includes: surrounding clamp and adjusting support 3;
[0016] The embracing clamp is made of metal material, and a silicone damping pad A8 is arranged on its inner annular surface. The covering area of the silicone damping pad A8 is not less than 85% of the area of the inner annular surface of the embracing clamp, and the thickness is 3mm-5mm; There are 4 threaded holes for installing and adjusting the support 3 evenly distributed on the outer annular surface in the circumferential direction; U-shaped grooves are provided on one end surface of the embracing clamp to provide enough space for the operation inside the embracing clamp; further, Effectively reduce the accuracy requirements of the center of the surrounding clamp for the opening of the end of the sensor, and it is convenient to implement the installation operation of the auxiliary support ...
PUM
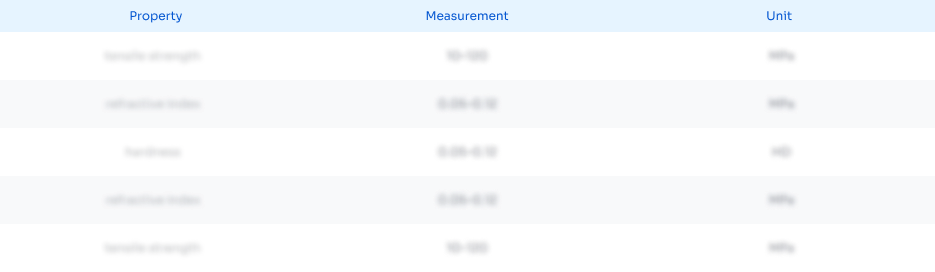
Abstract
Description
Claims
Application Information

- R&D
- Intellectual Property
- Life Sciences
- Materials
- Tech Scout
- Unparalleled Data Quality
- Higher Quality Content
- 60% Fewer Hallucinations
Browse by: Latest US Patents, China's latest patents, Technical Efficacy Thesaurus, Application Domain, Technology Topic, Popular Technical Reports.
© 2025 PatSnap. All rights reserved.Legal|Privacy policy|Modern Slavery Act Transparency Statement|Sitemap|About US| Contact US: help@patsnap.com