Material strip packaging machine
A packaging machine and tape technology, applied in the direction of welding/welding/cutting items, manufacturing tools, welding equipment, etc., can solve the problems of increasing production costs, waste materials, reducing production efficiency, etc., to improve production efficiency and prevent feeding errors Problems, Effects of Strong Market Competitiveness
- Summary
- Abstract
- Description
- Claims
- Application Information
AI Technical Summary
Problems solved by technology
Method used
Image
Examples
Embodiment Construction
[0013] For further illustrating the present invention, now cooperate with accompanying drawing to elaborate:
[0014] Such as figure 1 As shown, the material tape packaging machine includes a material rack group, a thermal welding group and a controller 6, and the material rack group includes a conveyor belt 1, a transmission device 2, an optical fiber 3, a reflective optical sensor 4 and a photoelectric converter 5, The transmission device is arranged under the conveyor belt and connected to the controller line, the optical fiber and the reflective light sensor are respectively arranged on the upper and lower sides of the conveyor belt and near the feeding position of the conveyor belt, and the optical fiber is arranged on the reflective optical sensor. Directly above the optical sensor, one end of the optical fiber is connected to the reflective optical sensor, the other end of the optical fiber is connected to the photoelectric converter, the photoelectric converter is conn...
PUM
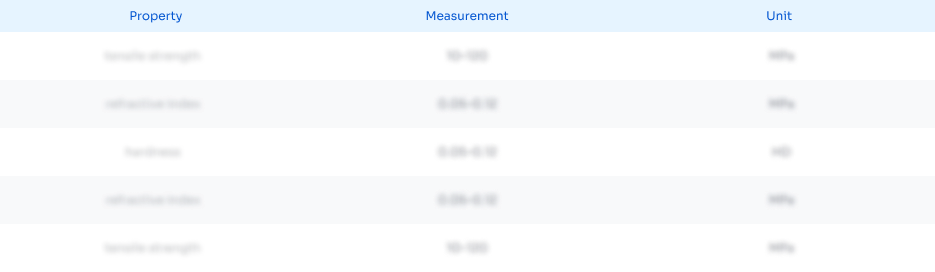
Abstract
Description
Claims
Application Information

- Generate Ideas
- Intellectual Property
- Life Sciences
- Materials
- Tech Scout
- Unparalleled Data Quality
- Higher Quality Content
- 60% Fewer Hallucinations
Browse by: Latest US Patents, China's latest patents, Technical Efficacy Thesaurus, Application Domain, Technology Topic, Popular Technical Reports.
© 2025 PatSnap. All rights reserved.Legal|Privacy policy|Modern Slavery Act Transparency Statement|Sitemap|About US| Contact US: help@patsnap.com