Friction stir welding stir-welding head provided with cutting edges
A friction stir welding and cutting edge technology, applied in welding equipment, non-electric welding equipment, metal processing equipment, etc., can solve problems such as uneven mixing of materials, achieve enhanced mechanical properties, improve welding quality and connection speed, and achieve sufficient mixing and stability. uniform effect
- Summary
- Abstract
- Description
- Claims
- Application Information
AI Technical Summary
Problems solved by technology
Method used
Image
Examples
Embodiment Construction
[0020] The present invention will be further described below in conjunction with the accompanying drawings and embodiments.
[0021] Such as Figure 1-4 shown.
[0022] A friction stir welding stirring head with a cutting edge, which mainly consists of a clamping handle 1, a transition cylinder 2, a shaft shoulder 3, a stirring needle 4, a cutting blade 5, a spiral groove 6, a blade groove 7 and a cutting edge 8 Composition, such as Figure 1-3 As shown, the clamping handle 1, the transition cylinder 2, the shaft shoulder 3 and the stirring needle 4 are sequentially connected, and the transition cylinder 2 is processed with several ring-shaped grooves that can reduce weight and facilitate heat dissipation. Processing has several spiral grooves 6 ( image 3 4 in the middle), the cross-sectional shape of the spiral groove 6 is U-shaped, and there are several blade grooves 7 on the left edge of the spiral groove 6, and several cutting blades 5 are installed in each blade groov...
PUM
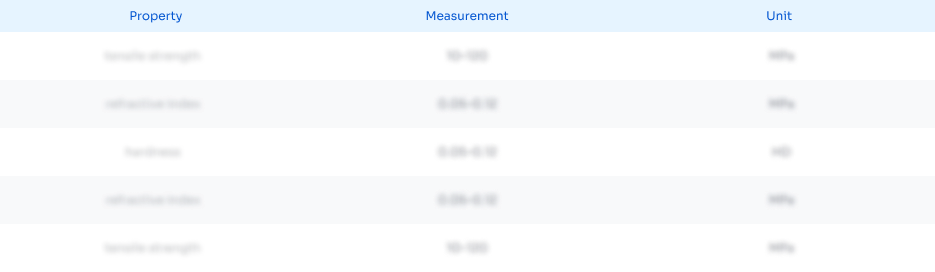
Abstract
Description
Claims
Application Information

- R&D
- Intellectual Property
- Life Sciences
- Materials
- Tech Scout
- Unparalleled Data Quality
- Higher Quality Content
- 60% Fewer Hallucinations
Browse by: Latest US Patents, China's latest patents, Technical Efficacy Thesaurus, Application Domain, Technology Topic, Popular Technical Reports.
© 2025 PatSnap. All rights reserved.Legal|Privacy policy|Modern Slavery Act Transparency Statement|Sitemap|About US| Contact US: help@patsnap.com