Tool for forming convex-concave multi-curvature type airplane skin product and composite forming technology
An aircraft skin and multi-curvature technology, which is applied in the field of sheet metal forming and manufacturing, can solve the problems of affecting the overall strength and rigidity of the part, increasing the difficulty of part positioning, and the inability to use the Mengla process, so as to reduce the number of divisions, Guaranteeing integrity and reducing production costs
- Summary
- Abstract
- Description
- Claims
- Application Information
AI Technical Summary
Problems solved by technology
Method used
Image
Examples
Embodiment Construction
[0039] In order to further understand the invention content, characteristics and effects of the present invention, the following examples are given, and detailed descriptions are as follows in conjunction with the accompanying drawings:
[0040] see Figure 1-Figure 6 , a tooling for forming convex-concave multi-curvature aircraft skin parts, comprising an upper template 3, a punch 1, a die 6 and a sealing ring 9, the die cavity is shaped like an inverted herringbone, and the screw It is connected with the upper template, and is guided and positioned with the upper template by the guide sleeve 4 and the guide pin 5, and the guide pin 5 and the die 6 are transition fit. The punch is composed of a pressing plate and a vertical rib integrated with the pressing plate. The head of the vertical rib of the punch is formed with a profile that matches the ridge of the product. It is fixed on the workbench 2 of the Mengla mold by fasteners to prevent the punch 1 from jumping during the...
PUM
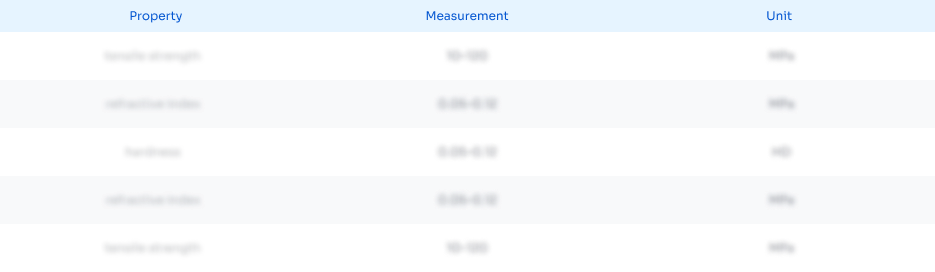
Abstract
Description
Claims
Application Information

- Generate Ideas
- Intellectual Property
- Life Sciences
- Materials
- Tech Scout
- Unparalleled Data Quality
- Higher Quality Content
- 60% Fewer Hallucinations
Browse by: Latest US Patents, China's latest patents, Technical Efficacy Thesaurus, Application Domain, Technology Topic, Popular Technical Reports.
© 2025 PatSnap. All rights reserved.Legal|Privacy policy|Modern Slavery Act Transparency Statement|Sitemap|About US| Contact US: help@patsnap.com