Robot hub brushless DC motor controller and control method thereof
A brushless DC motor and control method technology, applied in the direction of speed/torque control of a single motor, can solve the problems of lack of availability and inability to popularize hub motors, and achieve improved response speed, reduced speed fluctuations, and simplified control algorithms Effect
- Summary
- Abstract
- Description
- Claims
- Application Information
AI Technical Summary
Problems solved by technology
Method used
Image
Examples
Embodiment
[0075] Such as figure 1 As shown, this embodiment provides a hub motor controller that applies a hub DC brushless motor to a robot hub drive system. The DC brushless motor forming a wheeled robot driver in the present invention is a common hub motor with three phases wire and 5 signal wires, 3 phase wires provide power for the motor, and 5 signal wires are respectively +5V, GND, Ha, Hb, and Hc to provide signals for the motor commutation. The invention does not modify the hub motor and uses it directly The original phase line and signal line are used as input, which can realize speed closed-loop control and position feedback. The specific structure is as follows:
[0076] Including a control circuit 10, a three-phase drive bridge circuit 20 for driving a brushless DC motor M, the signal output terminal of the control circuit 10 is connected to the three-phase drive bridge circuit 20, and also includes a Hall sensor 30, the Hall The acquisition signal input end of the sensor 3...
PUM
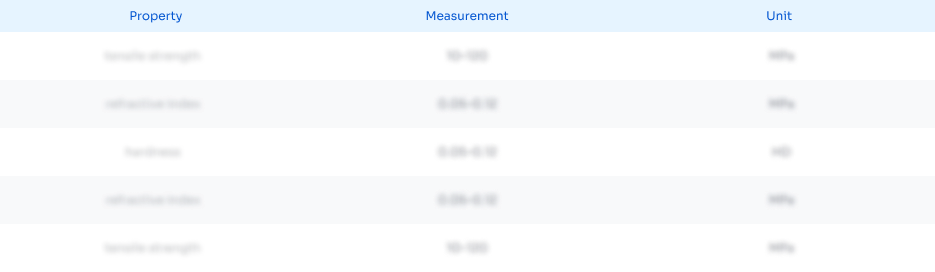
Abstract
Description
Claims
Application Information

- Generate Ideas
- Intellectual Property
- Life Sciences
- Materials
- Tech Scout
- Unparalleled Data Quality
- Higher Quality Content
- 60% Fewer Hallucinations
Browse by: Latest US Patents, China's latest patents, Technical Efficacy Thesaurus, Application Domain, Technology Topic, Popular Technical Reports.
© 2025 PatSnap. All rights reserved.Legal|Privacy policy|Modern Slavery Act Transparency Statement|Sitemap|About US| Contact US: help@patsnap.com