Fully automatic back cover powder filling system and process
A fully automatic, powder filling technology, applied in structural parts, circuits, electrical components, etc., can solve the problems of human body hazards, flying lead powder, easy damage, etc., to change the production mode, facilitate use and maintenance, and ensure life. Effect
- Summary
- Abstract
- Description
- Claims
- Application Information
AI Technical Summary
Problems solved by technology
Method used
Image
Examples
Embodiment Construction
[0069] Embodiments of the present invention are further described below in conjunction with accompanying drawings:
[0070] Such as figure 1 and figure 2 As shown, the automatic back cover powder filling system includes weighing powder mixing device Ⅰ, powder mixing elevator Ⅱ, quantitative powder lowering screw Ⅲ, several automatic powder filling machines Ⅳ, several low-pressure pulse dust collectors Ⅵ, weighing powder mixing device Ⅰ Connect the powder mixing elevator II, the powder mixing elevator II is connected to the automatic powder filling machine IV through the quantitative powder screw III, and the automatic powder filling machine IV is correspondingly connected to the low-pressure pulse dust collector VI, the automatic powder filling machine IV and the low-pressure pulse dust collector The device Ⅵ is connected with the powder filling screw Ⅴ;
[0071] Such as image 3 and Figure 4 As shown, the lead-acid battery automatic back cover powder filling system incl...
PUM
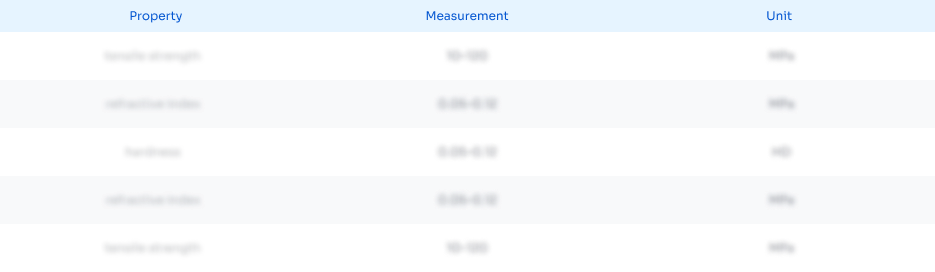
Abstract
Description
Claims
Application Information

- R&D
- Intellectual Property
- Life Sciences
- Materials
- Tech Scout
- Unparalleled Data Quality
- Higher Quality Content
- 60% Fewer Hallucinations
Browse by: Latest US Patents, China's latest patents, Technical Efficacy Thesaurus, Application Domain, Technology Topic, Popular Technical Reports.
© 2025 PatSnap. All rights reserved.Legal|Privacy policy|Modern Slavery Act Transparency Statement|Sitemap|About US| Contact US: help@patsnap.com