Sine-cosine encoder high precision signal processing system and method
A technology of sine and cosine encoder and signal processing, which can be used in instruments, conversion sensor output, measurement devices, etc., and can solve problems such as inability to meet higher resolution requirements.
- Summary
- Abstract
- Description
- Claims
- Application Information
AI Technical Summary
Problems solved by technology
Method used
Image
Examples
Embodiment 1
[0048] 1. Incremental rotary encoder signal processing principle
[0049] Under ideal conditions, the incremental rotary encoder outputs two sine and cosine signals with a phase difference of 90 degrees between A and B. When the encoder rotates in the positive direction, the B output signal phase lags the A signal by 90 degrees; on the contrary, when the encoder rotates in the opposite direction, the A output signal phase lags the B signal by 90 degrees. When the encoder rotates in the forward direction, the signal waveform is output, such as Figure 8 as shown, Figure 8 Output signal waveform diagram for the positive rotation of the encoder.
[0050] The initial signal of the encoder needs to be converted and processed before information such as the motor angle position can be obtained. In terms of signal processing, the encoder output signal is divided into two paths, such as Figure 9 as shown, Figure 9 It is a functional block diagram of the rotary encoder signal pr...
Embodiment 2
[0081] Assuming practical application:
[0082] 1. The encoder resolution is 2048 lines;
[0083] 2. The motor speed is 3000rpm;
[0084] 3. The feed rate of the screw rod per revolution of the motor is 5mm, that is, 5mm / r;
[0085] 4. The feed rate resolution reaches 0.0001mm, and the corresponding mechanical angle is 360 / (5 / 0.0001)=0.0072°=25.92″.
[0086] Let the encoder subdivision multiple be N, then: It is obtained that N>24.4, that is, the minimum 25 multiplier. Note: Since the frequency of the encoder interface unit has been multiplied by four, in order to achieve the ideal resolution, it needs to be multiplied by seven times, so that the overall subdivision multiple reaches 28 times.
[0087] When the rotational speed is 3000rpm, such as Figure 8 As shown, the frequency of the encoder output sine and cosine signals is:
[0088] Fine interpolation calculation formula:
[0089] Calculation formula of mechanical rotation angle:
[0090] Speed calculatio...
PUM
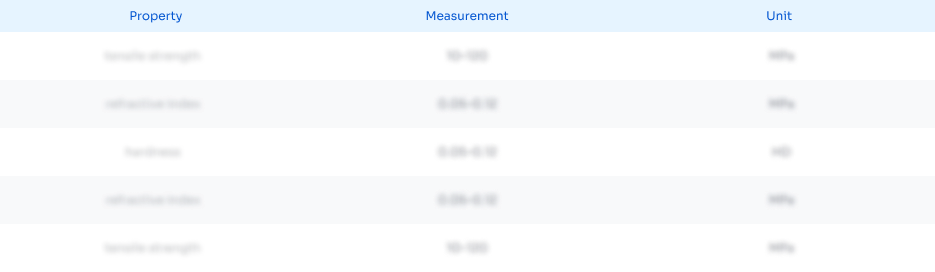
Abstract
Description
Claims
Application Information

- R&D
- Intellectual Property
- Life Sciences
- Materials
- Tech Scout
- Unparalleled Data Quality
- Higher Quality Content
- 60% Fewer Hallucinations
Browse by: Latest US Patents, China's latest patents, Technical Efficacy Thesaurus, Application Domain, Technology Topic, Popular Technical Reports.
© 2025 PatSnap. All rights reserved.Legal|Privacy policy|Modern Slavery Act Transparency Statement|Sitemap|About US| Contact US: help@patsnap.com