Self-balancing drilling and pulling-out mechanism with real-time bit pressure monitoring function
A self-balancing, real-time monitoring technology, applied in percussion drilling, rotary drilling, rotary drilling rigs, etc., can solve problems such as increased cost, large cumulative error, complex overall structure, etc., to avoid unbalanced force , avoiding the distortion of drilling pressure and improving the pull-out force
- Summary
- Abstract
- Description
- Claims
- Application Information
AI Technical Summary
Problems solved by technology
Method used
Image
Examples
Embodiment Construction
[0027] see Figure 1 to Figure 4 , shows the self-balancing drilling and pulling mechanism of the present invention with the function of real-time monitoring of the weight on bit.
[0028] The self-balancing drilling and pulling mechanism with the function of real-time monitoring of drilling pressure includes a primary fixed fuselage 14, a secondary oil cylinder feeding fuselage 15 and a power head support plate 16, and the primary fixed fuselage 14 is passed through a bolt It is installed on the drilling rig or the drilling rig frame in a fixed way, and then fixed. The feed body 15 of the secondary oil cylinder is telescopically arranged in the primary fixed body 14 through the oil cylinder, so that it can be stretched through the expansion and contraction of the oil cylinder. Drive the secondary oil cylinder to feed the fuselage 15 to move up and down relative to the primary fixed fuselage 14. The power head support plate 16 is located on the front side of the primary fixed ...
PUM
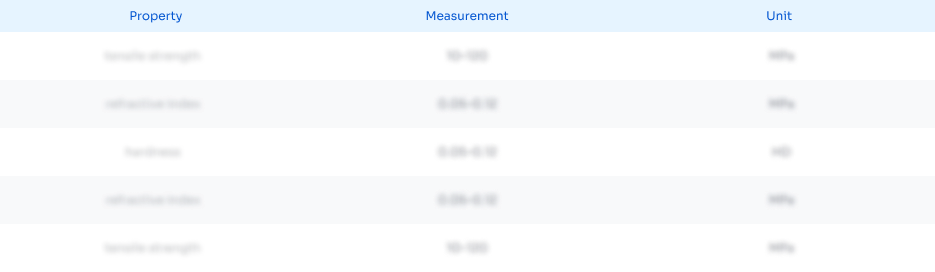
Abstract
Description
Claims
Application Information

- R&D
- Intellectual Property
- Life Sciences
- Materials
- Tech Scout
- Unparalleled Data Quality
- Higher Quality Content
- 60% Fewer Hallucinations
Browse by: Latest US Patents, China's latest patents, Technical Efficacy Thesaurus, Application Domain, Technology Topic, Popular Technical Reports.
© 2025 PatSnap. All rights reserved.Legal|Privacy policy|Modern Slavery Act Transparency Statement|Sitemap|About US| Contact US: help@patsnap.com