Transduction unit for ultrasonic transducer
A technology of ultrasonic transducer and transducer unit, which is applied in the direction of fluid using vibration, can solve the problems of reducing transducer efficiency, etc., and achieve the effect of improving transducer efficiency, good fit and stable working performance.
- Summary
- Abstract
- Description
- Claims
- Application Information
AI Technical Summary
Problems solved by technology
Method used
Image
Examples
Embodiment 1
[0030] like figure 1 and figure 2 As shown, the transducer unit of the ultrasonic transducer provided by the embodiment of the present invention includes a sealed indium steel shell and a piezoelectric ceramic ring 1 arranged in the indium steel shell, wherein the piezoelectric ceramic ring 1 includes a piezoelectric ceramic ring 1 An electric ceramic ring body, and an inner silver layer inside the piezoelectric ceramic ring body and an outer silver layer outside the piezoelectric ceramic ring body, and the outer silver layer is arranged close to the indium steel shell.
[0031] Compared with the traditional transducing unit, the oil medium is removed between the piezoelectric ceramic ring 1 and the shell in this embodiment, which improves the transducing efficiency. Meanwhile, the outer silver layer of the piezoelectric ceramic ring 1 is close to the indium steel shell, The heat generated by the piezoelectric ceramic ring 1 is dissipated through the indium steel shell, and ...
Embodiment 2
[0043] like Figure 4 and Figure 5 As shown, the second embodiment is basically the same as the first embodiment, and the similarities will not be repeated. The difference is that the casing 3 is a cylindrical structure with openings at both ends. When assembling, the cylindrical The casing 4 is sleeved on the outside of the piezoelectric ceramic ring 1 , and then two covers 5 are respectively covered on the two ends of the casing 4 .
[0044] Preferably, an aviation plug is arranged on one of the covers 5 .
[0045] In summary, the transducing unit of the ultrasonic transducer provided by the present invention removes the oil medium between the piezoelectric ceramic ring and the housing, thereby improving the transducing efficiency, and at the same time, the outer silver layer of the piezoelectric ceramic ring is closely attached to the The indium steel shell allows the heat generated by the piezoelectric ceramic ring to dissipate through the indium steel shell. Without af...
PUM
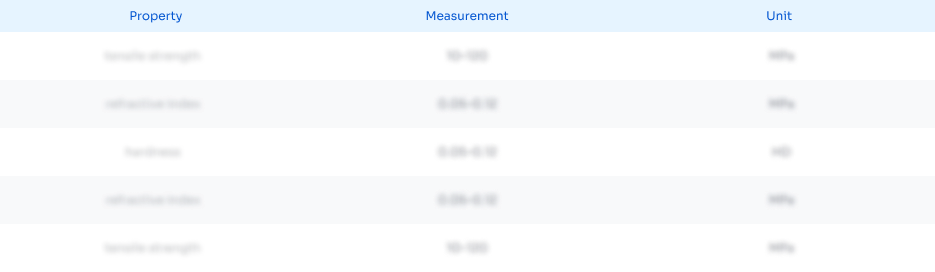
Abstract
Description
Claims
Application Information

- Generate Ideas
- Intellectual Property
- Life Sciences
- Materials
- Tech Scout
- Unparalleled Data Quality
- Higher Quality Content
- 60% Fewer Hallucinations
Browse by: Latest US Patents, China's latest patents, Technical Efficacy Thesaurus, Application Domain, Technology Topic, Popular Technical Reports.
© 2025 PatSnap. All rights reserved.Legal|Privacy policy|Modern Slavery Act Transparency Statement|Sitemap|About US| Contact US: help@patsnap.com