Fully coating ultrathin liquid absorption core and production method
A production method and a liquid absorbing core technology, which are applied in the field of volatilization, can solve the problems of inability to realize the production and cutting of a composite non-woven core body, inability to be covered by a polymer resin, and discomfort for users, so as to improve production efficiency and reduce Thickness, effect of reducing manufacturing cost
- Summary
- Abstract
- Description
- Claims
- Application Information
AI Technical Summary
Problems solved by technology
Method used
Image
Examples
Embodiment 1
[0011] Embodiment 1: with reference to attached figure 1 . An all-encompassing ultra-thin liquid-absorbing core, including a cladding layer 4, on the cladding layer 4 is provided with one or more layers of fluffed non-woven fabrics and polymer water-absorbent resin distributed on the fluffed non-woven fabrics Superimposed liquid-absorbing layers 1 and 2, the covering layer 3 is located on the liquid-absorbing layer, and the edge of the covering layer 4 is laminated on the covering layer 3 to form an all-inclusive ultra-thin liquid-absorbing core, which is heat-pressed or ultrasonically welded . The thickness of SAP applied on each layer of fluffed non-woven fabric depends on the amount of liquid absorbed.
[0012] The all-inclusive ultra-thin liquid-absorbent cores distributed in the composite non-woven fabric are distributed in strips with spacing and the spacing part is the bonding and cutting part. The bonding method can be ultrasonic bonding, electric heating fusion bond...
Embodiment 2
[0013] Embodiment 2: on the basis of embodiment 1, with reference to appended figure 2 . A diversion layer 5 is provided on the covering layer 3 or on the covering layer 4. The purpose of the diversion layer is to accelerate the diffusion and absorption of the liquid. Absorbent core.
Embodiment 3
[0014] Embodiment 3: On the basis of Embodiment 1 or 2, there is a small amount of glue on the polymer water-absorbing resin layer between the multi-layer fluffed non-woven fabrics.
PUM
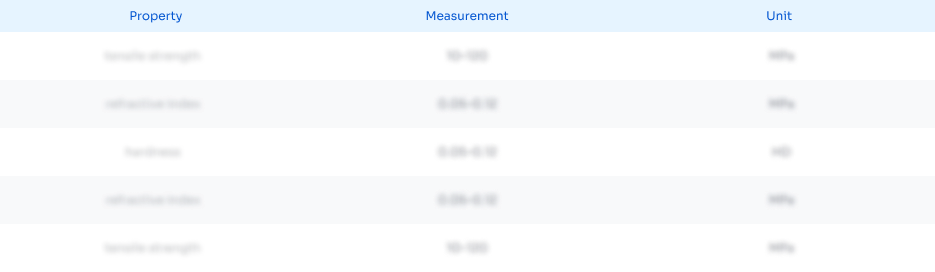
Abstract
Description
Claims
Application Information

- R&D
- Intellectual Property
- Life Sciences
- Materials
- Tech Scout
- Unparalleled Data Quality
- Higher Quality Content
- 60% Fewer Hallucinations
Browse by: Latest US Patents, China's latest patents, Technical Efficacy Thesaurus, Application Domain, Technology Topic, Popular Technical Reports.
© 2025 PatSnap. All rights reserved.Legal|Privacy policy|Modern Slavery Act Transparency Statement|Sitemap|About US| Contact US: help@patsnap.com