Double-axis synchronous movement control device and method based on feedback of laser displacement sensor
A technology of laser displacement and synchronous movement, which is applied in the direction of using feedback control, etc., can solve the problems that the height consistency of the gantry frame cannot be guaranteed, the gantry frame or drive components are damaged, and the degree of synchronous feed is reduced, so as to avoid zero point setting and errors Analysis, fast dynamic response, and flexible detection methods
- Summary
- Abstract
- Description
- Claims
- Application Information
AI Technical Summary
Problems solved by technology
Method used
Image
Examples
Embodiment 1
[0040] Such as figure 1 and figure 2 As shown, this embodiment provides a dual-axis synchronous motion control device based on laser displacement sensor feedback, including a dual-axis synchronous motion control device body, a displacement detection system and a control component;
[0041] The body of the two-axis synchronous motion control device includes a first drive mechanism, a second drive mechanism, a first linear motion platform 1, a second linear motion platform 2, and a test bench 3. The first drive mechanism constitutes one of the axes, and the first The linear motion platform 1 moves on this axis; the second drive mechanism constitutes another axis, the second linear motion platform 2 moves on this axis, and the synchronous motion of the first linear motion platform 1 and the second linear motion platform 2 is It is a two-axis synchronous movement;
[0042] The first driving mechanism includes a first servo motor 4, a first coupling 5 and a first ball screw 6 co...
PUM
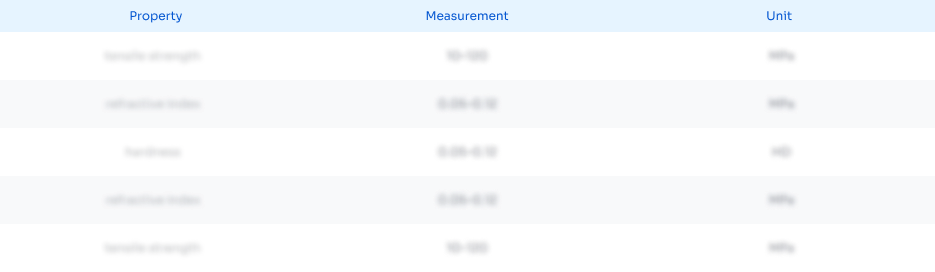
Abstract
Description
Claims
Application Information

- Generate Ideas
- Intellectual Property
- Life Sciences
- Materials
- Tech Scout
- Unparalleled Data Quality
- Higher Quality Content
- 60% Fewer Hallucinations
Browse by: Latest US Patents, China's latest patents, Technical Efficacy Thesaurus, Application Domain, Technology Topic, Popular Technical Reports.
© 2025 PatSnap. All rights reserved.Legal|Privacy policy|Modern Slavery Act Transparency Statement|Sitemap|About US| Contact US: help@patsnap.com