Gear case fault detection method combining vibration and sound wave monitoring
A fault detection and gearbox technology, applied in the field of detection, can solve the problems of inaccurate signals, complex vibration signals, low signal-to-noise ratio, etc., and achieve the effect of accurate data and reasonable operation
- Summary
- Abstract
- Description
- Claims
- Application Information
AI Technical Summary
Problems solved by technology
Method used
Image
Examples
Embodiment Construction
[0023] The present invention will be described in further detail below in conjunction with the accompanying drawings and specific embodiments.
[0024] Depend on figure 1 and figure 2 As can be seen from the flow diagram in the gearbox fault detection method of the present invention combined with vibration and sound wave monitoring, it includes a vibration signal fault detection system and an acoustic signal fault detection system, and the signal generators of the two systems are all installed on the gear case; The specific steps of the gearbox fault detection method are as follows:
[0025] 1) The acceleration sensor in the vibration signal fault detection system is adsorbed on the gearbox casing, the acoustic sensor in the sound wave signal fault detection system is installed outside the gearbox, and the speed sensor is installed on the gear shaft;
[0026] 2) Set signal conditioning and data acquisition equipment outside the gearbox, and electrically connect the accelera...
PUM
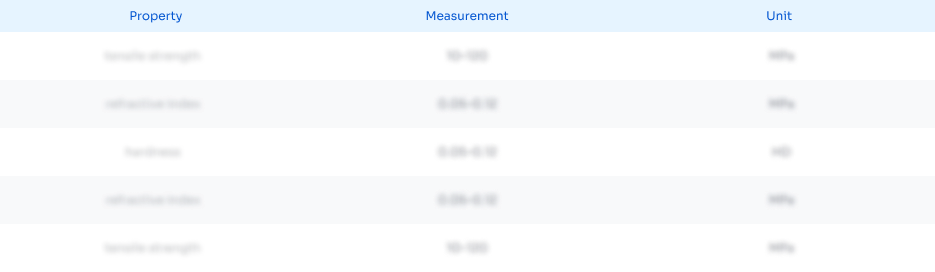
Abstract
Description
Claims
Application Information

- R&D
- Intellectual Property
- Life Sciences
- Materials
- Tech Scout
- Unparalleled Data Quality
- Higher Quality Content
- 60% Fewer Hallucinations
Browse by: Latest US Patents, China's latest patents, Technical Efficacy Thesaurus, Application Domain, Technology Topic, Popular Technical Reports.
© 2025 PatSnap. All rights reserved.Legal|Privacy policy|Modern Slavery Act Transparency Statement|Sitemap|About US| Contact US: help@patsnap.com