Precision casting bearing steel
A technology of precision casting and bearing steel, applied in the field of bearing steel, can solve the problems of complex heat treatment process, difficult production process, fatigue cracks, etc., to improve the solid solution strength and corrosion resistance, good mechanical properties and fatigue strength, good Effects of hardness and wear resistance
- Summary
- Abstract
- Description
- Claims
- Application Information
AI Technical Summary
Problems solved by technology
Method used
Image
Examples
Embodiment 1
[0022] Embodiment 1: A kind of precision casting bearing steel, it is made up of the following components by weight percentage: C: 0.95%, Si: 0.15%, Mn: 0.55%, S: 0.035%, Cr: 14%, P: 0.01 %, Al: 0.020%, N: 0.30%, Mo: 0.8%, and the balance is Fe and unavoidable impurities. The precision casting bearing steel is quenched at 910°C, tempered at 165°C, and tempered. It is tempered martensite, and eutectic carbides are dispersedly distributed on the tempered martensite matrix.
Embodiment 2
[0023] Embodiment 2: A kind of precision casting bearing steel, it is made up of the following components by weight percentage: C: 0.99%, Si: 0.20%, Mn: 0.65%, S: 0.04%, Cr: 15%, P: 0.015 %, Al: 0.025%, N: 0.35%, Mo: 0.9%, and the balance is Fe and unavoidable impurities. The precision casting bearing steel is quenched at 990°C, tempered at 165°C, and tempered. It is tempered martensite, and eutectic carbides are dispersedly distributed on the tempered martensite matrix.
Embodiment 3
[0024] Embodiment 3: A kind of precision casting bearing steel, it is made up of the following components by weight percentage: C: 1.02%, Si: 0.25%, Mn: 0.75%, S: 0.05%, Cr: 17%, P: 0.02 %, Al: 0.035%, N: 0.40%, Mo: 1.0%, and the balance is Fe and unavoidable impurities. The precision casting bearing steel is quenched at 1000°C, tempered at 165°C, and tempered. It is tempered martensite, and eutectic carbides are dispersedly distributed on the tempered martensite matrix.
PUM
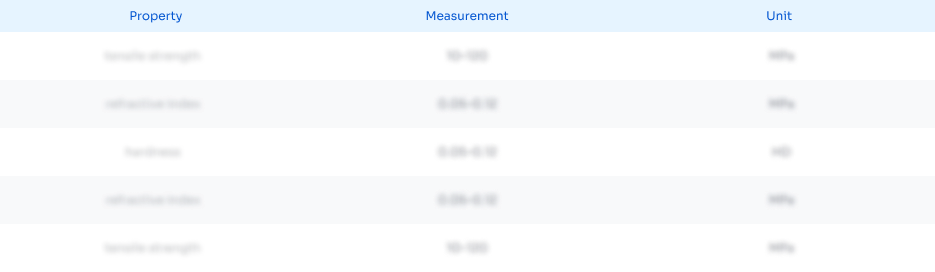
Abstract
Description
Claims
Application Information

- R&D
- Intellectual Property
- Life Sciences
- Materials
- Tech Scout
- Unparalleled Data Quality
- Higher Quality Content
- 60% Fewer Hallucinations
Browse by: Latest US Patents, China's latest patents, Technical Efficacy Thesaurus, Application Domain, Technology Topic, Popular Technical Reports.
© 2025 PatSnap. All rights reserved.Legal|Privacy policy|Modern Slavery Act Transparency Statement|Sitemap|About US| Contact US: help@patsnap.com