A method and device for controlling laser peening parameters and monitoring blade surface roughness
A surface roughness and laser peening technology, which is applied in the field of controlling laser peening parameters to monitor the surface roughness of blades, can solve the problems of performance loss, aero-engine safety, reliability and fatigue strength reduction, and weaken the mechanical properties of blades. Achieve the effects of improving fatigue life, ensuring consistency, accurate prediction and control
- Summary
- Abstract
- Description
- Claims
- Application Information
AI Technical Summary
Problems solved by technology
Method used
Image
Examples
Embodiment 1
[0024] Such as Figure 1-5 As shown, a method for controlling the parameters of laser peening to monitor the surface roughness of a blade includes the following steps:
[0025] Step 1: Use the surface roughness measuring instrument (10) to measure the surface roughness of the variable cross-section thin-walled complex blade (5) before the laser shot peening through the transmission mirror (4) to obtain the measured value before the treatment. The measured value before processing is transmitted to the computer control system (1) through the information acquisition system (11);
[0026] Step 2: Computer control system (1) According to the required surface roughness accuracy requirements of the variable cross-section thin-walled complex blade (5), the flat top variation and roughness of the laser peening beam built in the computer control system (1) In the database of the correspondence relationship between the linear interpolation methods, determine the laser peening parameters that...
Embodiment 2
[0036] Such as Figure 1-5 As shown, a method for controlling the parameters of laser peening to monitor the surface roughness of a blade includes the following steps:
[0037] Step 1: Use the surface roughness measuring instrument (10) to measure the surface roughness of the variable cross-section thin-walled complex blade (5) before the laser shot peening through the transmission mirror (4) to obtain the measured value before the treatment. The measured value before processing is transmitted to the computer control system (1) through the information acquisition system (11);
[0038] Step 2: Computer control system (1) According to the required surface roughness accuracy requirements of the variable cross-section thin-walled complex blade (5), the flat top variation and roughness of the laser peening beam built in the computer control system (1) In the database of the correspondence relationship between the linear interpolation methods, determine the laser peening parameters that...
Embodiment 3
[0048] Such as Figure 1-5 As shown, a method for controlling the parameters of laser peening to monitor the surface roughness of a blade includes the following steps:
[0049] Step 1: Use the surface roughness measuring instrument (10) to measure the surface roughness of the variable cross-section thin-walled complex blade (5) before the laser shot peening through the transmission mirror (4) to obtain the measured value before the treatment. The measured value before processing is transmitted to the computer control system (1) through the information acquisition system (11);
[0050] Step 2: Computer control system (1) According to the required surface roughness accuracy requirements of the variable cross-section thin-walled complex blade (5), the flat top variation and roughness of the laser peening beam built in the computer control system (1) In the database of the correspondence relationship between the linear interpolation methods, determine the laser peening parameters that...
PUM
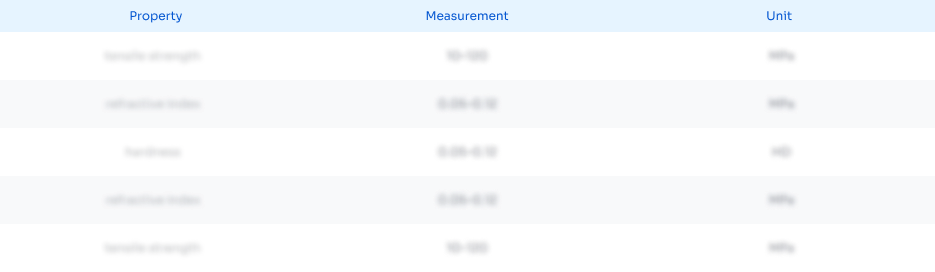
Abstract
Description
Claims
Application Information

- R&D Engineer
- R&D Manager
- IP Professional
- Industry Leading Data Capabilities
- Powerful AI technology
- Patent DNA Extraction
Browse by: Latest US Patents, China's latest patents, Technical Efficacy Thesaurus, Application Domain, Technology Topic, Popular Technical Reports.
© 2024 PatSnap. All rights reserved.Legal|Privacy policy|Modern Slavery Act Transparency Statement|Sitemap|About US| Contact US: help@patsnap.com