A growth process for yag crystal
A crystal and process technology, applied in the field of laser crystal growth technology, can solve the problems of short effective use length of crystals, crystal dislocation scattering, long growth period, etc. Effect
- Summary
- Abstract
- Description
- Claims
- Application Information
AI Technical Summary
Problems solved by technology
Method used
Image
Examples
Embodiment 1
[0028] A kind of growth technique for YAG crystal, comprises the following steps:
[0029] Step 1. Select a non-defective crystal head, and start vacuuming the resistance furnace with YAG raw materials to 6×10 -3 Pa, and then fill the resistance furnace with a protective gas, the protective gas is a mixture of argon and carbon dioxide, the filling method is to first fill the furnace with argon, so that the pressure in the furnace is 20KPa, and then fill Inject 4KPa of carbon dioxide gas;
[0030] Step 2. After step 1 is completed, heat up the material, control the heating rate at 388°C / h, and raise the temperature to 1975°C;
[0031] Step 3. Preheat the selected non-defective crystal heads to 1820°C for standby;
[0032] Step 4. After the YAG raw material in the resistance furnace is completely melted, homogenize at a constant temperature for 4 hours;
[0033] After step 5 and step 4 are completed, lower the preheated crystal head to contact the raw material solution and st...
Embodiment 2
[0040] Embodiment two is the same as embodiment one, and its difference is that the growth process of YAG crystal growth comprises the following steps:
[0041] Step 1. Select a non-defective crystal head, and start vacuuming the resistance furnace with YAG raw materials to 6×10 -3 Pa, and then fill the resistance furnace with a protective gas, the protective gas is a mixture of argon and carbon dioxide, the filling method is to fill the furnace with argon first, so that the pressure in the furnace is 23KPa, and then fill Inject 4.5KPa of carbon dioxide gas;
[0042] Step 2. After step 1 is completed, heat up the material, control the heating rate at 390°C / h, and raise the temperature to 1970°C;
[0043] Step 3. Preheat the selected non-defective crystal head to 1800°C for standby;
[0044] Step 4. After the YAG raw material in the resistance furnace is completely melted, homogenize at a constant temperature for 5 hours;
[0045] After step 5 and step 4 are completed, lower...
Embodiment 3
[0050] Embodiment three is the same as embodiment one and embodiment two, and its difference is that, the growth technique of YAG crystal comprises the following steps:
[0051] Step 1. Select a non-defective crystal head, and start vacuuming the resistance furnace with YAG raw materials to 6×10 -3 Pa, and then fill the resistance furnace with a protective gas, the protective gas is a mixture of argon and carbon dioxide, the filling method is to first fill the furnace with argon, so that the pressure in the furnace is 22KPa, and then fill Inject 4KPa of carbon dioxide gas;
[0052] Step 2. After step 1 is completed, heat up the material, control the heating rate at 380°C / h, and raise the temperature to 1990°C;
[0053] Step 3. Preheat the selected non-defective crystal head to 1850°C for standby;
[0054] Step 4. After the YAG raw material in the resistance furnace is completely melted, homogenize at a constant temperature for 3 hours;
[0055] After step 5 and step 4 are com...
PUM
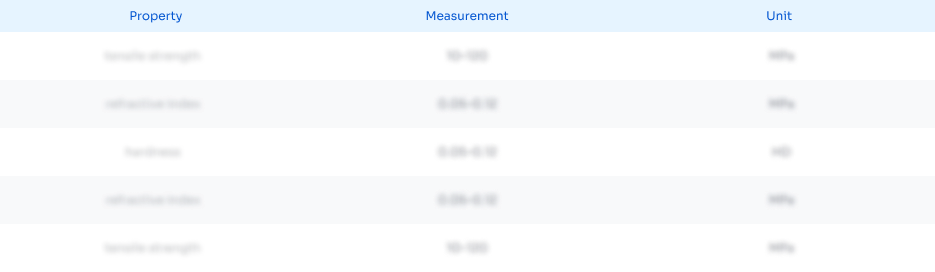
Abstract
Description
Claims
Application Information

- R&D Engineer
- R&D Manager
- IP Professional
- Industry Leading Data Capabilities
- Powerful AI technology
- Patent DNA Extraction
Browse by: Latest US Patents, China's latest patents, Technical Efficacy Thesaurus, Application Domain, Technology Topic, Popular Technical Reports.
© 2024 PatSnap. All rights reserved.Legal|Privacy policy|Modern Slavery Act Transparency Statement|Sitemap|About US| Contact US: help@patsnap.com