Controlled-release pesticide granules and preparation method therefor
A technology of controlled-release pesticides and granules, applied in the field of pesticides, can solve problems such as harsh process requirements and soil solvent pollution, and achieve the effects of wide application range, pollution reduction, and high quality stability
- Summary
- Abstract
- Description
- Claims
- Application Information
AI Technical Summary
Problems solved by technology
Method used
Examples
Embodiment 1
[0042] The first layer of active ingredients: clothianidin 4kg, polyvinylpyrrolidone 6.4kg, kaolin and clay 140kg; the second layer of active ingredients: monosultap 16kg, dextrin 64kg, borax 9.6kg, kaolin, clay and calcium carbonate 760kg .
[0043] The preparation method comprises the following steps:
[0044] (1) Preparation of the first layer of active ingredients: Stir and mix clothianidin and polyvinylpyrrolidone in the first layer of active ingredients evenly, add kaolin and clay to prepare mixed material A;
[0045] (2) Preparation of the second layer of active ingredients: Stir and mix the monosultap, dextrin and borax in the second layer of active ingredients, and add kaolin and clay to prepare the mixed material B;
[0046] (3) Put the mixed material A in the granulation tray, open the granulation tray, spray water to start granulation, heat up after granules appear, the temperature is 70~90°C, after the mixed material A is completely made into granules and solidif...
Embodiment 2
[0051] The first active ingredient layer: Thiamethoxam 10kg, sodium carboxymethylcellulose 15kg, kaolin and clay 300kg; the second active ingredient layer: cyfluthrin 15kg, dextrin 64kg, borax 9.6kg, kaolin, clay and gypsum 578.23 kg; protective layer: dextrin 325g, borax 48.75g, pigment 2g, kaolin and clay 7.8kg.
[0052] The preparation method comprises the following steps:
[0053] (1) Preparation of the first layer of active ingredients: Stir and mix thiamethoxam and polyvinylpyrrolidone in the first layer of active ingredients, and add kaolin and clay to prepare the mixed material A;
[0054] (2) Preparation of the second active ingredient layer: Stir and mix the cyfluthrin, dextrin and borax in the active ingredients of the second layer evenly, add kaolin and clay to prepare the mixed material B;
[0055] (3) Put the mixed material A in the granulation tray, open the granulation tray, spray water to start granulation, heat up after granules appear, the temperature is 70...
Embodiment 3
[0060] The first active ingredient layer: monosultap 5kg, abamectin 50kg, sodium carboxymethyl cellulose 55kg, kaolin and clay 300kg; the second layer of active ingredients: monosultap 5kg, abamectin 50kg, paste Refined 165kg, borax 24.75kg, kaolin, clay and calcium carbonate 345.25kg.
[0061] The preparation method comprises the following steps:
[0062] (1) Preparation of the first layer of active ingredients: Stir and mix the monosultap, abamectin and sodium carboxymethylcellulose in the first layer of active ingredients, and add kaolin and clay to prepare the mixed material A;
[0063] (2) Preparation of the second layer of active ingredients: Stir and mix the monosultap, abamectin, dextrin and borax in the second layer of active ingredients, and add kaolin and clay to prepare the mixed material B;
[0064] (3) Put the mixed material A in the granulation tray, open the granulation tray, spray water to start granulation, heat up after granules appear, the temperature is 7...
PUM
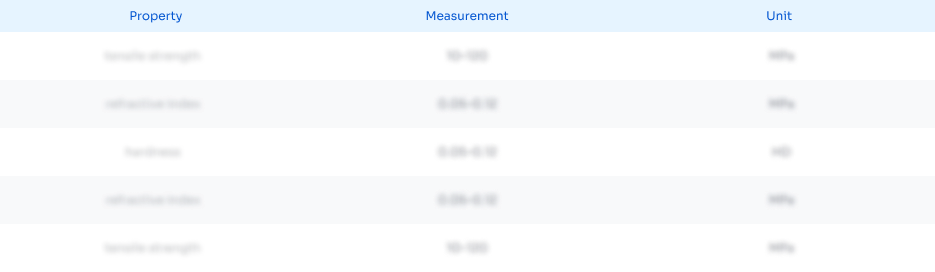
Abstract
Description
Claims
Application Information

- R&D Engineer
- R&D Manager
- IP Professional
- Industry Leading Data Capabilities
- Powerful AI technology
- Patent DNA Extraction
Browse by: Latest US Patents, China's latest patents, Technical Efficacy Thesaurus, Application Domain, Technology Topic, Popular Technical Reports.
© 2024 PatSnap. All rights reserved.Legal|Privacy policy|Modern Slavery Act Transparency Statement|Sitemap|About US| Contact US: help@patsnap.com