Method for preparing copper gallium sulfide photoelectric thin film from copper sulfate
A photoelectric thin film, copper gallium sulfide technology, applied in the direction of photovoltaic power generation, circuits, electrical components, etc., can solve the problems of high preparation cost and complicated process route, and achieve the effect of low production cost, low requirements for equipment and high production efficiency
- Summary
- Abstract
- Description
- Claims
- Application Information
AI Technical Summary
Benefits of technology
Problems solved by technology
Method used
Examples
Embodiment 1
[0026] a. Cleaning of the glass substrate: the glass substrate is cleaned as described above, and the size of the substrate is 20mm×20mm.
[0027] b. 1.66 parts of Cu 2 SO 4 ·5H 2 O, 1.71 parts Ga(NO 3 ) 3 ·xH 2 O and 1.0 CH 3 CSNH 2 Put into 13.3 parts of deionized water and mix evenly, and use ultrasonic vibration for more than 30 minutes to make the substances in the solution evenly mix.
[0028]c. Drop the above solution onto the glass substrate placed on the homogenizer, start the homogenizer, make the homogenizer rotate at 300 rpm for 5 seconds, and rotate at 2150 rpm for 15 seconds, so that the dripped solution is coated After uniformity, after the substrate is dried, the above-mentioned solution is repeatedly dripped and spin-coated, and then dried again. This is repeated 3 to 5 times, and a precursor thin film sample with a certain thickness is obtained on the glass substrate.
[0029] d. Put the precursor thin film sample obtained by the above process into a ...
PUM
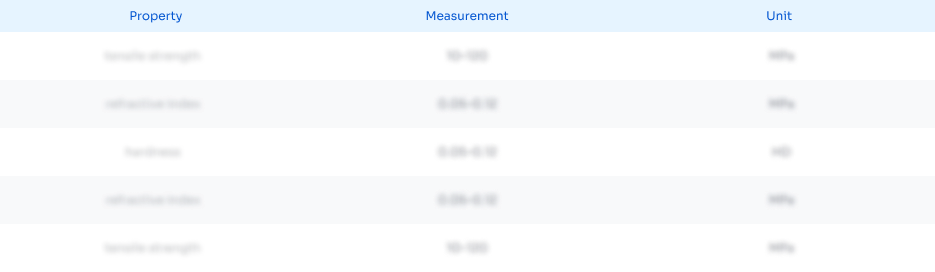
Abstract
Description
Claims
Application Information

- R&D Engineer
- R&D Manager
- IP Professional
- Industry Leading Data Capabilities
- Powerful AI technology
- Patent DNA Extraction
Browse by: Latest US Patents, China's latest patents, Technical Efficacy Thesaurus, Application Domain, Technology Topic, Popular Technical Reports.
© 2024 PatSnap. All rights reserved.Legal|Privacy policy|Modern Slavery Act Transparency Statement|Sitemap|About US| Contact US: help@patsnap.com