Short-screw double material extruding machine
An extruder and screw technology, which is applied in the field of short-screw twin-material extruders, can solve the problems of insufficient extruder capacity and shortened delivery cycle, and achieve the effect of low replacement and maintenance cost and shortened length.
- Summary
- Abstract
- Description
- Claims
- Application Information
AI Technical Summary
Problems solved by technology
Method used
Image
Examples
Embodiment 1
[0033] As shown in the figure, a short-screw double-material extruder includes a first barrel 1 and a first screw 2, the first screw 2 is rotatably arranged in the first barrel 1, and the first screw 2 includes a central through-hole Screw body, the screw body has a left support part 2.3, the outer cylinder of the first screw rod 2 is provided with a first outer screw edge 2.1 between the left support part 2.3 and the right end, in the center hole from the corresponding inner hole of the right end There is a first internal thread 2.2 from the position, and the injection shaft 8 fits in the first internal thread 2.2;
[0034] As shown in the figure, the helical directions of the first outer flight 2.1 and the first inner flight 2.2 are set in opposite directions, when the first outer flight 2.1 is a right-handed flight, the first inner flight 2.2 is a left-handed flight, so Only in this way can it be ensured that when the first screw 2 rotates counterclockwise, the conveying di...
Embodiment 2
[0045] The right end of the screw body of the first screw 2, the first right baffle plate 10 and the annular inlet channel between the right end center through hole of the screw body of the first screw and the second barrel 3 constitute a mixing section, and the discharge ramp The outlet of the hole 3.1 is located in the mixing section, and a mixing impeller 22 is rotated in the mixing section, and the mixing impeller 22 mixes the materials in the screw conveying section A and the screw conveying section D. The mixing impeller 22 is rotatably arranged in the first right baffle plate 10, and the mixing impeller 22 is driven by a separate rotary driving device. The mixing impeller 22 fully mixes the materials in the mixing screw conveying section A and the screw conveying section D, and then enters the inner screw plasticizing section B from the annular inlet. The blade profile of the mixing impeller 22 is conical, and the large end of the conical ring is facing the annular chan...
PUM
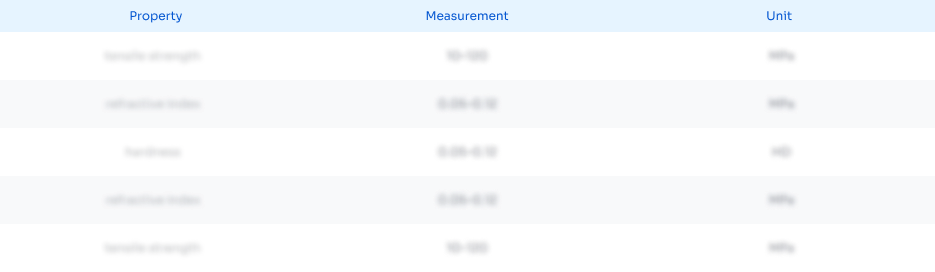
Abstract
Description
Claims
Application Information

- Generate Ideas
- Intellectual Property
- Life Sciences
- Materials
- Tech Scout
- Unparalleled Data Quality
- Higher Quality Content
- 60% Fewer Hallucinations
Browse by: Latest US Patents, China's latest patents, Technical Efficacy Thesaurus, Application Domain, Technology Topic, Popular Technical Reports.
© 2025 PatSnap. All rights reserved.Legal|Privacy policy|Modern Slavery Act Transparency Statement|Sitemap|About US| Contact US: help@patsnap.com