Gypsum hollow block and semi-dry production method of same
A hollow block and production method technology, applied in the field of hollow block production for building houses, can solve the problems of large storage yard, long cycle, high cost, etc., and achieve the effect of large storage yard and high cost
- Summary
- Abstract
- Description
- Claims
- Application Information
AI Technical Summary
Problems solved by technology
Method used
Examples
Embodiment 1
[0022] A semi-dry method for producing gypsum hollow blocks, comprising the following steps:
[0023] 1) Prepare 24Kg of water at 5°C, then slowly add 0.1Kg of methylcellulose and 0.2Kg of carboxymethylcellulose, and add 1Kg of quicklime while stirring Homogenously, a water mixture is obtained;
[0024] 2) Weigh 80Kg of building gypsum powder prepared by 0.6Kg citric acid, 0.2Kg naphthalenesulfonate formaldehyde condensate, 10Kg fly ash and desulfurized gypsum and mix evenly to obtain a mixed powder;
[0025] 3) Add the mixed powder of step 2) and the water mixture of step 1) into the mixer for high-speed stirring at a stirring speed of 500-600r / min to obtain a semi-dry gypsum colloid, and then distribute the material evenly to the gypsum through the gypsum mortar conveying device The hollow block forming machine is combined with mold cavity, external pressure is formed, and then hydraulic pressure is ejected from the cavity to obtain a gypsum hollow block.
[0026] Accordin...
Embodiment 2
[0028] A semi-dry method for producing gypsum hollow blocks, comprising the following steps:
[0029] 1) Prepare 27Kg of water at 10°C, then slowly add 0.2Kg of methylcellulose and 0.3Kg of carboxymethylcellulose, and add 1.5Kg of slag during the melting process of methylcellulose and carboxymethylcellulose, while Stir well to obtain a water mixture;
[0030] 2) Weigh 90Kg of building gypsum powder prepared by 0.8Kg citric acid, 0.4Kg naphthalenesulfonate formaldehyde condensate, 15Kg fly ash and titanium gypsum and mix evenly to obtain a mixed powder;
[0031] 3) Add the mixed powder of step 2) and the water mixture of step 1) into the mixer for high-speed stirring at a stirring speed of 500-600r / min to obtain a semi-dry gypsum colloid, and then distribute the material evenly to the gypsum through the gypsum mortar conveying device The hollow block forming machine is combined with mold cavity, external pressure is formed, and then hydraulic pressure is ejected from the cavit...
Embodiment 3
[0034] A semi-dry method for producing gypsum hollow blocks, comprising the following steps:
[0035] 1) Prepare 36Kg of water at 20°C, then slowly add 0.15Kg of methyl cellulose and 0.2Kg of carboxymethyl cellulose, and add 2Kg of cement while stirring Homogenously, a water mixture is obtained;
[0036] 2) Weigh 0.7Kg of citric acid, 0.5Kg of naphthalenesulfonate formaldehyde condensate, 20Kg of fly ash and 90Kg of building gypsum powder prepared by phosphogypsum production and mix evenly to obtain a mixed powder;
[0037] 3) Add the mixed powder of step 2) and the water mixture of step 1) into the mixer for high-speed stirring at a stirring speed of 500-600r / min to obtain a semi-dry gypsum colloid, and then distribute the material evenly to the gypsum through the gypsum mortar conveying device The hollow block forming machine is combined with mold cavity, external pressure is formed, and then hydraulic pressure is ejected from the cavity to obtain a gypsum hollow block.
...
PUM
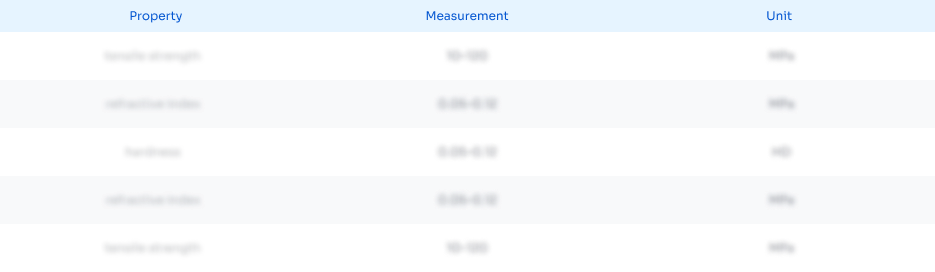
Abstract
Description
Claims
Application Information

- R&D
- Intellectual Property
- Life Sciences
- Materials
- Tech Scout
- Unparalleled Data Quality
- Higher Quality Content
- 60% Fewer Hallucinations
Browse by: Latest US Patents, China's latest patents, Technical Efficacy Thesaurus, Application Domain, Technology Topic, Popular Technical Reports.
© 2025 PatSnap. All rights reserved.Legal|Privacy policy|Modern Slavery Act Transparency Statement|Sitemap|About US| Contact US: help@patsnap.com