Internal high pressure-forming method for special-shaped tube
A forming method and internal high-pressure technology, which is applied in the field of internal high-pressure forming of special-shaped pipe fittings, can solve the problems of large wall thickness changes and easy cracking, and achieve the effects of gentle wall thickness changes, avoiding cracks, and improving economic benefits
- Summary
- Abstract
- Description
- Claims
- Application Information
AI Technical Summary
Problems solved by technology
Method used
Image
Examples
Embodiment Construction
[0038] The present invention will be further described below in conjunction with specific embodiment and accompanying drawing, set forth more details in the following description so as to fully understand the present invention, but the present invention can obviously be implemented in many other ways different from this description, Those skilled in the art can make similar promotions and deductions based on actual application situations without violating the connotation of the present invention, so the content of this specific embodiment should not limit the protection scope of the present invention.
[0039] image 3 It is a flow chart of the internal high-pressure forming method of special-shaped pipe fittings according to an embodiment of the present invention. Such as image 3 As shown, the internal high pressure forming method adopts the method of one mold and multiple parts, and its process mainly includes:
[0040] Firstly, step S301 is executed to analyze and confir...
PUM
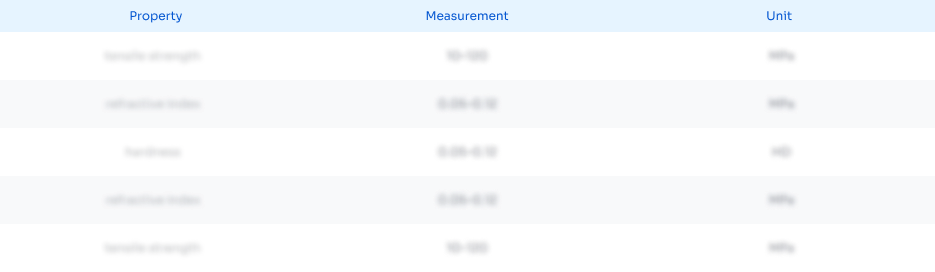
Abstract
Description
Claims
Application Information

- R&D
- Intellectual Property
- Life Sciences
- Materials
- Tech Scout
- Unparalleled Data Quality
- Higher Quality Content
- 60% Fewer Hallucinations
Browse by: Latest US Patents, China's latest patents, Technical Efficacy Thesaurus, Application Domain, Technology Topic, Popular Technical Reports.
© 2025 PatSnap. All rights reserved.Legal|Privacy policy|Modern Slavery Act Transparency Statement|Sitemap|About US| Contact US: help@patsnap.com