Nano indentation testing device under stretch-four-point bending preload
A four-point bending and nano-indentation technology, which is applied in the direction of measuring devices, instruments, scientific instruments, etc., can solve the problems of large dispersion, unfavorable function expansion, and lack of methods for evaluating the accuracy of mechanical parameter testing, and achieves compact structure, volume small effect
- Summary
- Abstract
- Description
- Claims
- Application Information
AI Technical Summary
Problems solved by technology
Method used
Image
Examples
Embodiment Construction
[0022] see Figure 1 to Figure 4 As shown, the present invention includes a tensile preload loading mechanism, a four-point bending preload loading mechanism and an in-situ nano-indentation testing mechanism.
[0023] The precision DC servo motor 36 in the tensile preload loading mechanism is fixedly installed on the test platform base 1 through the motor flange 38, and forms a first-stage deceleration and commutation with the worm gear II 39. The bi-directional ball screw nut pair 37 converts the rotary motion of the worm gear worm pair II 39 into a synchronous two-way linear motion, and then drives the specimen fixture support seat Ⅰ14 and fixture support seat Ⅱ30 installed on the nut pair to realize synchronous two-way linear motion, and the specimen fixture The support base I14 and the clamp support base II30 are installed on the linear guide rail 29 of the stretching mechanism below, wherein the clamp II34 is connected with the force sensor 31 of the stretching mechanism ...
PUM
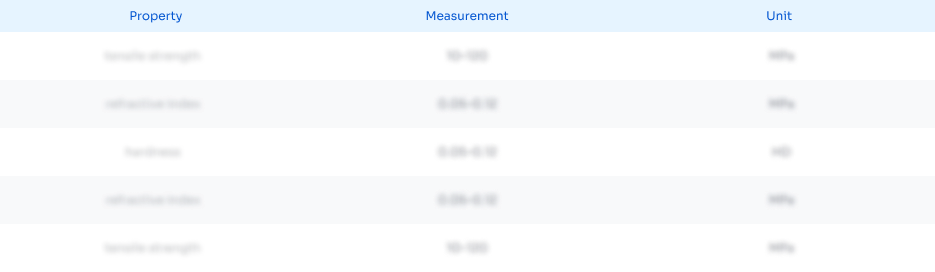
Abstract
Description
Claims
Application Information

- R&D
- Intellectual Property
- Life Sciences
- Materials
- Tech Scout
- Unparalleled Data Quality
- Higher Quality Content
- 60% Fewer Hallucinations
Browse by: Latest US Patents, China's latest patents, Technical Efficacy Thesaurus, Application Domain, Technology Topic, Popular Technical Reports.
© 2025 PatSnap. All rights reserved.Legal|Privacy policy|Modern Slavery Act Transparency Statement|Sitemap|About US| Contact US: help@patsnap.com