A method of positioning and boring holes for aircraft canard assembly by using a servo system
A servo system and positioning hole technology, which is applied to aircraft parts, boring/drilling, transportation and packaging, etc., can solve the problems of difficult finishing, low positioning efficiency, poor positioning accuracy, etc., and improve efficiency and reliability , Accuracy assurance and efficiency improvement, the effect of accuracy improvement
- Summary
- Abstract
- Description
- Claims
- Application Information
AI Technical Summary
Problems solved by technology
Method used
Image
Examples
Embodiment 1
[0033] When positioning the outer canard support beam, combined with the attached Figure 1-2 Shown, a kind of adopt servo system to the method for assembling positioning boring of aircraft canard, described servo system comprises servo motor 2, position detection sensor and PLC logic controller, and described servo motor 2 is installed in the boring machine that is used for boring On the workbench 3, the boring machine workbench 3 is installed on the boring machine bed 1; the PLC logic controller controls the action of the servo motor 2 by issuing a positioning parameter feed command, and the servo motor 2 controls the The precise movement of the boring machine table 3 along the boring machine bed 1, the position detection sensor can detect the actual position information of the boring machine table 3 and transmit it to the PLC logic controller, wherein the method includes the following steps:
[0034] Step 1: Put the outer canard support beam on the boring machine table 3, i...
Embodiment 2
[0038] When positioning the inner canard support beam, combined with the attached figure 1 and 3 Shown, a kind of adopt servo system to the method for assembling positioning boring of aircraft canard, described servo system comprises servo motor 2, position detection sensor and PLC logic controller, and described servo motor 2 is installed in the boring machine that is used for boring On the boring machine table 3, the boring machine table 3 is installed on the boring machine bed 1; the PLC logic controller controls the action of the servo motor 2 by issuing a positioning parameter feed command, and the servo motor 2 controls The precise movement of the boring machine table 3 along the boring machine bed 1, the position detection sensor can detect the actual position information of the boring machine table 3 and transmit it to the PLC logic controller, wherein the method includes the following steps:
[0039]Step 1: Put the inner canard support beam on the boring machine tabl...
Embodiment 3
[0043] When positioning and boring the canard support beam inside the aircraft, combined with the attached figure 1 And attached Figure 4 Shown, a kind of adopt servo system to the method for assembling positioning boring of aircraft canard, described servo system comprises servo motor 2, position detection sensor and PLC logic controller, and described servo motor 2 is installed in the boring machine that is used for boring On the boring machine table 3, the boring machine table 3 is installed on the boring machine bed 1; the PLC logic controller controls the action of the servo motor 2 by issuing a positioning parameter feed command, and the servo motor 2 controls The precise movement of the boring machine table 3 along the boring machine bed 1, the position detection sensor can detect the actual position information of the boring machine table 3 and transmit it to the PLC logic controller, wherein the method includes the following steps:
[0044] Step 1: Put the inner can...
PUM
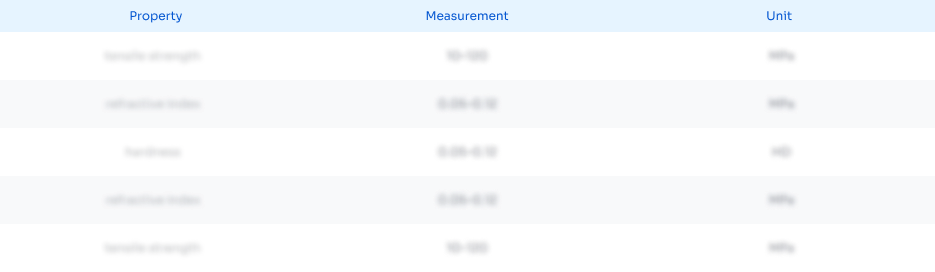
Abstract
Description
Claims
Application Information

- Generate Ideas
- Intellectual Property
- Life Sciences
- Materials
- Tech Scout
- Unparalleled Data Quality
- Higher Quality Content
- 60% Fewer Hallucinations
Browse by: Latest US Patents, China's latest patents, Technical Efficacy Thesaurus, Application Domain, Technology Topic, Popular Technical Reports.
© 2025 PatSnap. All rights reserved.Legal|Privacy policy|Modern Slavery Act Transparency Statement|Sitemap|About US| Contact US: help@patsnap.com