Heat stabilizer for PVC (polyvinyl chloride) and preparation method and application thereof
A technology of heat stabilizer and solvent, applied in the field of heat stabilizer for PVC and its preparation, can solve problems such as use limitation, and achieve the effect of overcoming poor heat resistance, reducing loss and enhancing compatibility
- Summary
- Abstract
- Description
- Claims
- Application Information
AI Technical Summary
Problems solved by technology
Method used
Image
Examples
Embodiment 1
[0025] (1) Dissolve 78.10 g (molecular weight: 390.51, 0.2 mol) of tungalin anhydride in 93.72 g of ethyl acetate, add it to the reaction vessel, and heat up to 25-60°C. Dissolve 24.41g (molecular weight: 137.14, 0.178mol) of p-aminobenzoic acid in 317.33g of ethyl acetate, add it dropwise to the reaction vessel, react at this temperature for 4 hours after the dropwise addition, spin evaporate, and dry in vacuo to obtain a solid product N-(3-Amino-benzoyl) tramamic acid.
[0026] (2) Add 26.38 g (molecular weight: 527.65, 0.05 mol) of N-(3-amino-benzoyl) temamic acid and 26.38 g of diethylene glycol monobutyl ether into the reaction vessel, and raise the temperature to 70°C. After completely dissolving, add 3.88g (molecular weight 81.39, 0.0475mol) zinc oxide or 2.58g (molecular weight 56.08, 0.046mol) calcium oxide in 2 batches, raise the temperature to 125°C, add 0.15g of glacial acetic acid dropwise, keep warm for 3h, pump Filtration and rotary evaporation to remove water ...
Embodiment 2
[0030] (1) Dissolve 78.10 g of tungalic anhydride in 78.10 g of ethyl acetate, add it into a reaction vessel, and heat up to 25-60°C. Dissolve 22.90 g of p-aminobenzoic acid in 343.50 g of ethyl acetate, and add it dropwise to the reaction vessel. After the dropwise addition, react at this temperature for 4 hours, rotary evaporate, and vacuum dry to obtain the solid product N-(3-amino- Benzoyl) tramamic acid.
[0031] (2) 26.38g of N-(3-amino-benzoyl) tungemamic acid, 7.91g of diethylene glycol monobutyl ether and 7.91g of odorless kerosene were added to the reaction vessel, and the temperature was raised to 70°C. After completely dissolving, add 3.70g of zinc oxide or 2.80g of calcium oxide in 3 batches, raise the temperature to 120°C, add 0.05g of hydrogen peroxide dropwise, keep warm for 3h, filter with suction, and remove water by rotary evaporation to obtain liquid N-(3-amino- Benzoyl) tramamic acid zinc salt or N-(3-amino-benzoyl) tramamic acid calcium salt.
[0032] (...
Embodiment 3
[0034] (1) Dissolve 78.10 g of tungalin anhydride in 117.15 g of acetone, add it into a reaction vessel, and raise the temperature to 25-60°C. 22.90g of p-aminobenzoic acid was dissolved in 458g of acetone, and was added dropwise to the reaction vessel. After the dropwise addition, it was reacted at this temperature for 4h, rotary evaporated, and dried in vacuo to obtain the solid product N-(3-amino-benzoic acid group ) Tongmamic acid.
[0035] (2) Add 26.38g of N-(3-amino-benzoyl) tiramamic acid and 7.91g of diethylene glycol monobutyl ether into the reaction vessel, and raise the temperature to 70°C. After completely dissolving, add 3.70g of zinc oxide or 2.80g of calcium oxide in 3 batches, raise the temperature to 120°C, add 0.05g of glacial acetic acid dropwise, keep warm for 3h, filter with suction, and remove water by rotary evaporation to obtain liquid N-(3-amino -Zinc salt of benzoyl)tramamic acid or calcium salt of N-(3-amino-benzoyl)tramamic acid.
[0036] (3) 6g ...
PUM
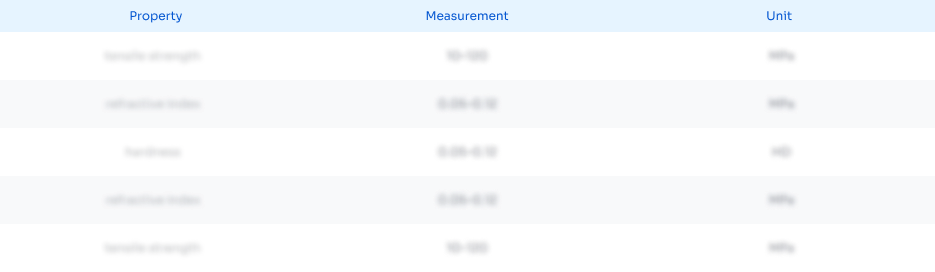
Abstract
Description
Claims
Application Information

- R&D
- Intellectual Property
- Life Sciences
- Materials
- Tech Scout
- Unparalleled Data Quality
- Higher Quality Content
- 60% Fewer Hallucinations
Browse by: Latest US Patents, China's latest patents, Technical Efficacy Thesaurus, Application Domain, Technology Topic, Popular Technical Reports.
© 2025 PatSnap. All rights reserved.Legal|Privacy policy|Modern Slavery Act Transparency Statement|Sitemap|About US| Contact US: help@patsnap.com