Overloaded five-core quick joint robot control system
A control system and robot technology, applied in the direction of program control manipulators, manipulators, manufacturing tools, etc., can solve the problems that cannot meet the requirements of high-precision SCARA robot systems, cannot meet the requirements of heavy-duty SCARA robot systems, and cannot meet the requirements of SCARA robot energy-saving systems. , to achieve the effects of strong program portability, convenient task change, and shortened development cycle
- Summary
- Abstract
- Description
- Claims
- Application Information
AI Technical Summary
Problems solved by technology
Method used
Image
Examples
Embodiment Construction
[0025] The following will clearly and completely describe the technical solutions in the embodiments of the present invention. Obviously, the described embodiments are only some of the embodiments of the present invention, rather than all the embodiments. Based on the embodiments of the present invention, all other embodiments obtained by persons of ordinary skill in the art without making creative efforts belong to the protection scope of the present invention.
[0026] see Figure 2 to Figure 7 , the embodiment of the present invention includes: a heavy-duty five-core fast joint robot control system, the robot is a SCARA robot based on a four-axis rare earth permanent magnet synchronous servo motor, that is, the joint robot is driven by a rare earth permanent magnet synchronous servo motor X 7 The robot arm rotates, the rare earth permanent magnet synchronous servo motor Y 8 is used to drive the robot arm rotation, the rare earth permanent magnet synchronous servo motor Z 9 ...
PUM
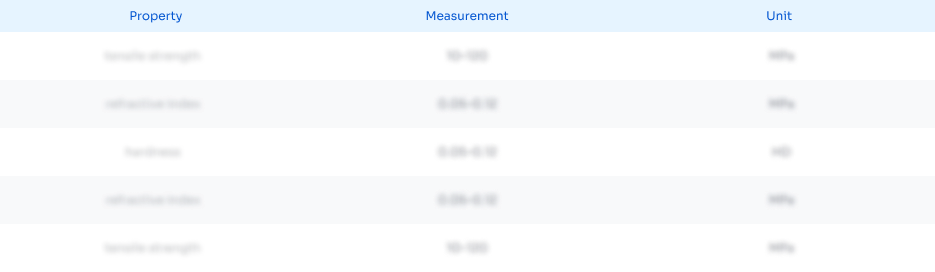
Abstract
Description
Claims
Application Information

- Generate Ideas
- Intellectual Property
- Life Sciences
- Materials
- Tech Scout
- Unparalleled Data Quality
- Higher Quality Content
- 60% Fewer Hallucinations
Browse by: Latest US Patents, China's latest patents, Technical Efficacy Thesaurus, Application Domain, Technology Topic, Popular Technical Reports.
© 2025 PatSnap. All rights reserved.Legal|Privacy policy|Modern Slavery Act Transparency Statement|Sitemap|About US| Contact US: help@patsnap.com