Method for dynamic characteristic simulation of numerically controlled machine tool and integration with numerical control system
A technology of CNC machine tools and CNC systems, which is applied in general control systems, control/regulation systems, instruments, etc., and can solve problems such as high price, limited test accuracy and anti-interference ability.
- Summary
- Abstract
- Description
- Claims
- Application Information
AI Technical Summary
Problems solved by technology
Method used
Image
Examples
Embodiment Construction
[0023]In order to meet the requirements of real-time calculation of the working state of the machine tool and input the calculation results into the CNC system quickly and effectively, firstly, through the multi-body rigid-flexible coupling real-time modeling system of the machine tool, finite element technology is used to realize the finite element mesh division of the machine tool related parts, and the zero The flexible body model of the component, which defines the flexible body model as a superelement substructure. And a high-efficiency, low-order calculation model is generated through super-element technology. In the modeling software, each flexible body substructure is coupled and connected, and the matrix equation of the machine tool dynamics multi-body rigid-flexible coupling model is established. Therefore, an online overall model of each real-time working state of the CNC machine tool (such as different feed positions, different feed speeds, etc.) is established. ...
PUM
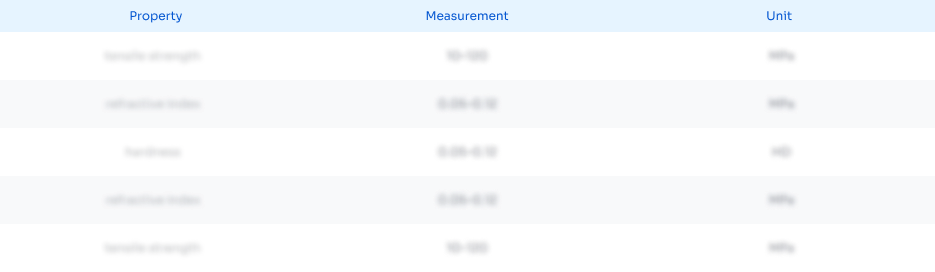
Abstract
Description
Claims
Application Information

- Generate Ideas
- Intellectual Property
- Life Sciences
- Materials
- Tech Scout
- Unparalleled Data Quality
- Higher Quality Content
- 60% Fewer Hallucinations
Browse by: Latest US Patents, China's latest patents, Technical Efficacy Thesaurus, Application Domain, Technology Topic, Popular Technical Reports.
© 2025 PatSnap. All rights reserved.Legal|Privacy policy|Modern Slavery Act Transparency Statement|Sitemap|About US| Contact US: help@patsnap.com