A heat loss test method for a thermal comprehensive test device
A technology of comprehensive testing and testing methods, applied in the testing of machines/structural components, measuring devices, instruments, etc., can solve the problems of difficult measurement, poor accuracy, and low accuracy, and achieve strong operability and accuracy High, precise results
- Summary
- Abstract
- Description
- Claims
- Application Information
AI Technical Summary
Problems solved by technology
Method used
Image
Examples
Embodiment 1
[0052] A heat loss test method of a thermal comprehensive test device of the present invention comprises the following steps,
[0053] a. Determine the heat loss test conditions
[0054] Determine the pressure and temperature of the reactor and the primary circuit system, the waste heat removal system, and the temperature of the pressurizer 4, that is, determine a working point, including the reactor and the primary circuit system, and the pressure of the waste heat discharge system is 15MPa, and the reactor and the primary circuit The temperature of the system is 300°C, and the temperature of the regulator 4 is 350°C.
[0055] b. Establish heat loss test conditions
[0056] b.1. According to the heat loss test conditions determined in step a, lay insulation cotton in the reactor, the primary loop system, and the secondary loop system, start the main pump 6 and the waste heat discharge pump 11, and put the main heat source simulator 1 into the reactor for simulation The devi...
Embodiment 2
[0066] Such as figure 1 As shown, the thermal comprehensive test device includes a reactor and a primary circuit system, a secondary circuit system, a waste heat removal system, and a cold source simulation system. The reactor and a primary circuit system include a main heat source simulator 1 and a secondary heat source simulator 2 , reactor simulator 3, pressurizer 4, steam generator simulation body 5, main pump 6, the main heat source simulator 1 is connected with reactor simulator 3, main pump 6, steam generator simulation body 5 in sequence, and the secondary heat source The simulator 2 is connected with the reactor simulator 3 and the steam generator simulation body 5 sequentially through the voltage stabilizer 4 .
[0067] Among them, the reactor and the primary loop system are also called the main system of the primary loop of the reaction. The function of the voltage stabilizer 4 in this system is to control the pressure of the coolant and prevent the core from deviat...
Embodiment 3
[0082] The present embodiment is as the comparative example of embodiment 1 and 2:
[0083] The heat loss test method of the existing thermal comprehensive test device will be described, including the following steps:
[0084] a. Determine the heat loss test conditions
[0085] Same operation as step a in Example 1.
[0086] b. Establish heat loss test conditions
[0087] The operation is the same as step b in Example 1.
[0088] c. Measure flow and temperature parameters
[0089] Keep the power of main heat source simulator 1 and secondary heat source simulator 2 constant, and stabilize the loop parameters for 20 minutes; measure the flow rate of main pump 6 and waste heat discharge pump 11, and measure reactor simulator 3, steam generator simulation body 5, and main pump 6. Equipment such as steam turbine simulator 8, waste heat discharge cooler 10, waste heat discharge pump 11, cold source simulator 13, and the inlet and outlet temperatures of pipelines between each devic...
PUM
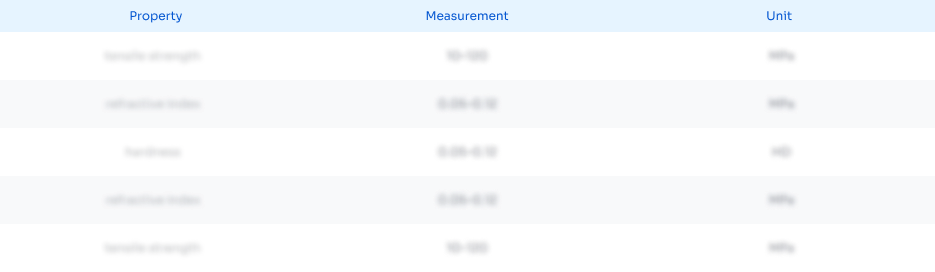
Abstract
Description
Claims
Application Information

- R&D Engineer
- R&D Manager
- IP Professional
- Industry Leading Data Capabilities
- Powerful AI technology
- Patent DNA Extraction
Browse by: Latest US Patents, China's latest patents, Technical Efficacy Thesaurus, Application Domain, Technology Topic, Popular Technical Reports.
© 2024 PatSnap. All rights reserved.Legal|Privacy policy|Modern Slavery Act Transparency Statement|Sitemap|About US| Contact US: help@patsnap.com