Zero Error Test of Angle Measuring System and Comprehensive Error Compensation Method
A technology of zero error and comprehensive error, which is applied in the field of angle measurement error testing and calibration, can solve the problems of insufficient zero error testing and deduction, significant compensation effect, and discounted compensation effect, so as to achieve good overall compensation effect and strong engineering The effect of applying value
- Summary
- Abstract
- Description
- Claims
- Application Information
AI Technical Summary
Problems solved by technology
Method used
Image
Examples
specific Embodiment 1
[0068] Specific embodiment 1 based on the polyhedral prism inductosynchronous angle measurement system zero error and subdivision error test (assuming that the number of pole pairs m of the precision measuring element is 360)
[0069] 1) Test system preparation.
[0070] cling to figure 1 As shown, the polygonal prism is installed on the shaft end of the measured shaft through tooling, and the autocollimator and the measured shaft are placed on the same base. Adjust the optical axis of the autocollimator to be at the same height as the axis of the prism, rotate the measured axis, and adjust the tower difference to the allowable range (≤100″).
[0071] 2) Test and calculate the relative zero error of 4 sets of 1° intervals.
[0072] a) Using a 72-sided prism to test the relative zero position error of 4 sets of 5° intervals. Start the test with the 0° output of the angle measurement system as the starting point. At this time, the reading of the autocollimator is cleared, and...
Embodiment 2
[0075] Embodiment 2 Error compensation based on the zero position error and subdivision error test of the inductive synchronizer angle measurement system based on the polyhedral prism
[0076] 1) Zero error calculation and compensation. After the odd and even zero position errors of any pair of poles are calculated by formula 1, the error compensation amount Δα caused by the zero position error in different intervals of any pair of poles is calculated as shown in Table 1 z , and directly subtract it from the current sampling angle of the angle measurement system, and record the angle output after deducting the zero error as θ1. Assuming that the current sampling angle of the goniometric system is 234.8710°, the calculation sequence number i in Table 1=234.
[0077] Table 1 Calculation error compensation amount Δα z
[0078]
[0079] 2) Subdivision error calculation and compensation. After compensating the influence of the zero position error as shown in step 1), take th...
PUM
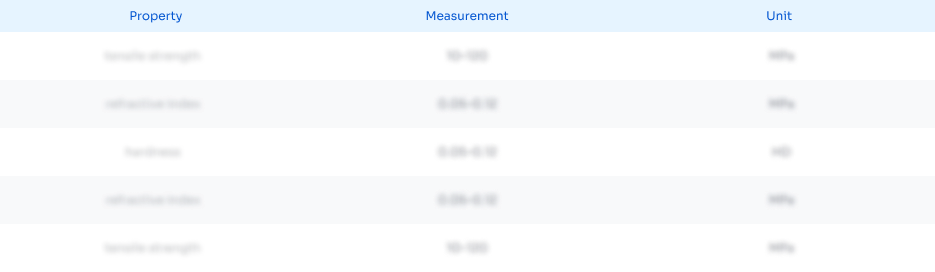
Abstract
Description
Claims
Application Information

- R&D
- Intellectual Property
- Life Sciences
- Materials
- Tech Scout
- Unparalleled Data Quality
- Higher Quality Content
- 60% Fewer Hallucinations
Browse by: Latest US Patents, China's latest patents, Technical Efficacy Thesaurus, Application Domain, Technology Topic, Popular Technical Reports.
© 2025 PatSnap. All rights reserved.Legal|Privacy policy|Modern Slavery Act Transparency Statement|Sitemap|About US| Contact US: help@patsnap.com