Attitude-orbit integrated control oriented multi-execution mechanism cooperative control distribution method
A technology with multiple actuators and distribution methods, applied in attitude control, non-electric variable control, control/regulation systems, etc., can solve the problems of less mutual cooperation and low fuel usage of thrusters, and achieve improved use efficiency and good expansion Effects on sex and flexibility
- Summary
- Abstract
- Description
- Claims
- Application Information
AI Technical Summary
Problems solved by technology
Method used
Image
Examples
specific Embodiment approach 1
[0018] Specific implementation mode one: as figure 1 and figure 2 As shown, a multi-actuator cooperative control distribution method for integrated control of attitude and orbit includes the following steps:
[0019] Step 1: According to the desired control force F c , using the thrust correction coefficient optimization model oriented to the minimum thrust distribution error, transform the thrust correction coefficient optimization model into a standard linear programming model, solve the desired thrust correction factor k, and calculate the output desired control force F m,c ;
[0020] Among them, the expected thrust correction factor k is to correct the expected thrust when the expected control quantity exceeds the output capability range of the actuator.
[0021] f m,c = kF c (16)
[0022] Step 2: For the thruster, control the torque T according to the expectation c and the output expected control force F obtained in step 1 m,c , using the hybrid optimization mod...
specific Embodiment approach 2
[0030] Specific implementation mode two: the difference between this implementation mode and specific implementation mode one is: the thrust correction coefficient optimization model in the step one is specifically:
[0031] Min J=-k (1)
[0032] St.Bu=kF c (2)
[0033] u i,min i i,max ,i=1,2,...,n (3)
[0034] where u i is the i-th thruster, n is the number of thrusters (representing a matrix with n columns), k is the thrust correction coefficient, B is the thrust control efficiency matrix of the thruster, u is the control command of the thruster, and J is the objective function.
[0035] Other steps and parameters are the same as those in Embodiment 1.
specific Embodiment approach 3
[0036] Specific implementation mode three: the difference between this implementation mode and specific implementation mode one or two is: in the step one, the specific form of converting the thrust correction coefficient optimization model into a standard linear programming model is:
[0037] D = D 3 × n - B F c ...
PUM
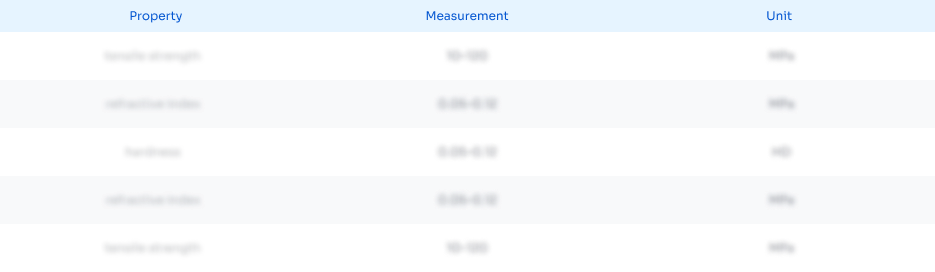
Abstract
Description
Claims
Application Information

- R&D
- Intellectual Property
- Life Sciences
- Materials
- Tech Scout
- Unparalleled Data Quality
- Higher Quality Content
- 60% Fewer Hallucinations
Browse by: Latest US Patents, China's latest patents, Technical Efficacy Thesaurus, Application Domain, Technology Topic, Popular Technical Reports.
© 2025 PatSnap. All rights reserved.Legal|Privacy policy|Modern Slavery Act Transparency Statement|Sitemap|About US| Contact US: help@patsnap.com