Electromechanical system multilayer reliability prediction method based on fuzzy evaluation
A technology of electromechanical systems and fuzzy judgments, applied in prediction, calculation, electrical digital data processing, etc., can solve problems such as the inability to distinguish the importance of system units
- Summary
- Abstract
- Description
- Claims
- Application Information
AI Technical Summary
Problems solved by technology
Method used
Image
Examples
Embodiment 1
[0045] Such as figure 1 As shown, a method for multi-level reliability prediction of electromechanical system based on fuzzy judgment. First, the electromechanical system is processed in a hierarchical structure; the hierarchy is divided from top to bottom, including system layer, sub-system layer, functional module layer, and basic functions The elements of each level are called units, the upper level is the parent unit level of the next level, and the next level is the child unit level of the previous level; and then the electromechanical system is multiplied from the bottom to the top. The calculation of the weight coefficient of the hierarchical unit and the reliability prediction. For electromechanical systems with different complexity, you can increase or decrease on the basis of the above 4 levels until the analysis needs are met. The method of weight coefficient calculation and reliability prediction includes the following steps:
[0046] Step 1. Sub-unit risk priority ...
Embodiment 2
[0075] Taking the electromechanical system of a ground high-mobility radar as an example, the above method is described in detail. The specific handling methods of this case are as follows:
[0076] Step 1. Hierarchical structure processing of electromechanical system
[0077] The electromechanical system is processed in a hierarchical structure, and the levels are divided from top to bottom, including the system layer, the sub-system layer, the function module layer and the basic function layer. Such as figure 2 As shown, the system layer is the radar electromechanical control system, the sub-system layer includes the leveling, erection and control sub-systems, the functional module layer includes functional modules such as bionic legs, support legs, and pitch, and the basic functional layer includes pin shafts, support leg structures, Basic units such as reducers.
[0078] Step 2. The calculation of the risk priority number of the bottom unit and the construction of the binary c...
PUM
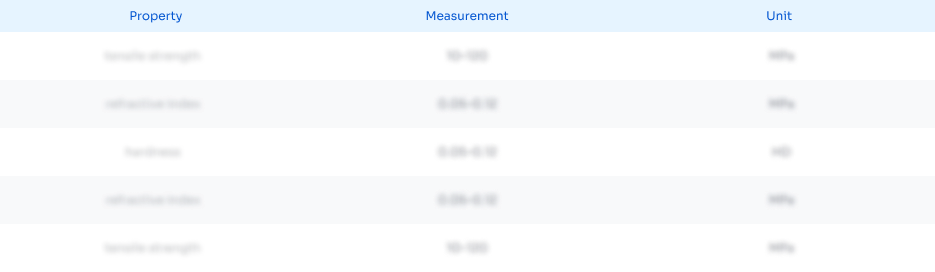
Abstract
Description
Claims
Application Information

- Generate Ideas
- Intellectual Property
- Life Sciences
- Materials
- Tech Scout
- Unparalleled Data Quality
- Higher Quality Content
- 60% Fewer Hallucinations
Browse by: Latest US Patents, China's latest patents, Technical Efficacy Thesaurus, Application Domain, Technology Topic, Popular Technical Reports.
© 2025 PatSnap. All rights reserved.Legal|Privacy policy|Modern Slavery Act Transparency Statement|Sitemap|About US| Contact US: help@patsnap.com