Accurate positioning and feeding device for tubular workpiece single end machining
A precise positioning and feeding device technology, applied in the direction of conveyors, conveyor objects, transportation and packaging, etc., can solve the problems of low clamping positioning accuracy, low degree of automation, cumbersome operation, etc., and achieve flexible and automatic motion. High, easy-to-operate effect
- Summary
- Abstract
- Description
- Claims
- Application Information
AI Technical Summary
Problems solved by technology
Method used
Image
Examples
Embodiment Construction
[0024] The present invention will be further described below in conjunction with the accompanying drawings:
[0025] like figure 1 and figure 2 As shown, the precise positioning feeding device for single-end processing of tubular workpieces includes base 1, first arch 2, second arch 3, three-jaw chuck 4, chuck drive cylinder 5, chuck drive motor 6, ball screw 7, Lead screw driving motor 8, linear guide rail 9, sliding seat 10, leading screw nut 11 and leading screw nut connecting plate 12.
[0026] The linear guide rail 9 is fixed on the base 1, the sliding seat 10 is set on the linear guide rail 9, the first arch 2 is fixed on the left end of the linear guide rail 9, the second arch 3 is fixed on the sliding seat 10, the first arch 2 and the The second arch 3 is provided with a circular through hole of equal size, and the diameters of the three-jaw chuck 4 and the tubular workpiece 31 are all smaller than the diameter of the circular through hole; the ball screw 7 is arran...
PUM
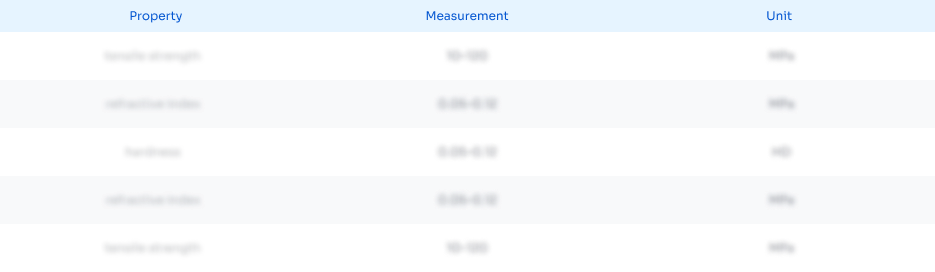
Abstract
Description
Claims
Application Information

- R&D
- Intellectual Property
- Life Sciences
- Materials
- Tech Scout
- Unparalleled Data Quality
- Higher Quality Content
- 60% Fewer Hallucinations
Browse by: Latest US Patents, China's latest patents, Technical Efficacy Thesaurus, Application Domain, Technology Topic, Popular Technical Reports.
© 2025 PatSnap. All rights reserved.Legal|Privacy policy|Modern Slavery Act Transparency Statement|Sitemap|About US| Contact US: help@patsnap.com