Redundant-driven friction stir welding parallel robot
A technology of friction stir welding and robots, which is applied in welding equipment, non-electric welding equipment, metal processing equipment, etc., can solve the problems of low rigidity and small working space, achieve high rigidity, high processing precision, and improve rigidity and precision performance Effect
- Summary
- Abstract
- Description
- Claims
- Application Information
AI Technical Summary
Problems solved by technology
Method used
Image
Examples
Embodiment 1
[0024] like figure 1 Shown: a 3-DOF parallel mechanism for friction stir welding, including frame 11, moving platform 5, stirring head 6 and four branches connecting the frame and moving platform; the stirring head used for processing Fixed on the moving platform; the first branch (this branch is a PRS type motion branch chain) and the third branch are arranged symmetrically to the moving platform; the second branch (this branch is a PRU type motion branch chain) and the fourth branch are symmetrical to the moving platform Arrangement; the hinge center points of the first branch, the second branch, the third branch and the fourth branch and the moving platform are evenly distributed around the moving platform and arranged in 90° equal parts to each other; the first branch and the third branch are respectively In turn, it includes the first moving pair 1P connected between the frame 11 and the moving platform (including the slider 12 and the guide rod fixed on the frame 11), th...
Embodiment 2
[0026] Embodiment two, such as figure 2 Shown: a 3-DOF parallel mechanism for friction stir welding, including frame 11, moving platform 5, stirring head 6 and four branches connecting the frame and moving platform; the stirring head used for processing Fixed on the moving platform; the first branch (the branch is the RPS type motion branch chain) and the third branch are arranged symmetrically to the moving platform; the second branch and the fourth branch are arranged symmetrically to the moving platform; the first branch, the second branch, The hinge center points of the third branch and the fourth branch and the moving platform are evenly distributed around the moving platform and are arranged equally at 90° to each other; Between the first rotating pair 1R, the first moving pair 1P (including the slider 12 and the first guide rod 15), the first guide rod 15 and the ball joint 1S; the second branch and the fourth branch respectively include connecting The second rotating...
Embodiment 3
[0028] Embodiment three, such as image 3 Shown: a 3-DOF parallel mechanism for friction stir welding, including frame 11, moving platform 5, stirring head 6 and four branches connecting the frame and moving platform; the stirring head used for processing Fixed on the moving platform; the first branch (the branch is the RRS type motion branch chain) and the third branch are arranged symmetrically to the moving platform; the second branch and the fourth branch are arranged symmetrically to the moving platform; the first branch, the second branch, The hinge center points of the third branch and the fourth branch and the moving platform are evenly distributed around the moving platform and arranged equally at 90° to each other; Between the third rotating pair 1R 1 , the third connecting rod 17, the fourth revolving pair 1R 2 , the fourth connecting rod 18 and the ball joint 1S; the second branch and the fourth branch respectively include the fifth rotating pair 2R connected betwe...
PUM
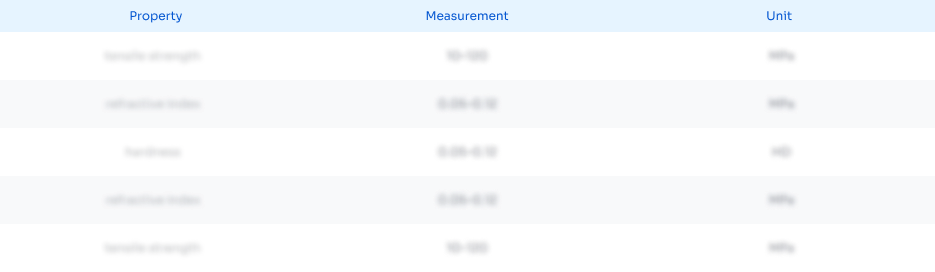
Abstract
Description
Claims
Application Information

- R&D
- Intellectual Property
- Life Sciences
- Materials
- Tech Scout
- Unparalleled Data Quality
- Higher Quality Content
- 60% Fewer Hallucinations
Browse by: Latest US Patents, China's latest patents, Technical Efficacy Thesaurus, Application Domain, Technology Topic, Popular Technical Reports.
© 2025 PatSnap. All rights reserved.Legal|Privacy policy|Modern Slavery Act Transparency Statement|Sitemap|About US| Contact US: help@patsnap.com