Pulse backflushing cleaning device and its gas ejector and filter device
A technology of pulse backflushing and dust removal device, which is applied in the fields of dispersed particle filtration, transportation and packaging, chemical instruments and methods, etc. It can solve the problems of more severe vibration of filter tubes, impact force of filter tubes, bridging of dust layers, etc., to achieve Uniform and thorough dust removal, increased air intake rate, and reduced vibration
- Summary
- Abstract
- Description
- Claims
- Application Information
AI Technical Summary
Problems solved by technology
Method used
Image
Examples
Embodiment Construction
[0025] In order to have a clearer understanding of the technical features, purposes and effects of the present invention, the specific implementation manners of the present invention will now be described in detail with reference to the accompanying drawings.
[0026] Figure 1a with 1b A gas ejector of a pulse back-blowing soot cleaning device provided by an embodiment of the present invention. The gas ejector includes an ejector body, and the ejector body includes an inlet portion 101, a neck portion 102 and an arched portion 103 connected to each other in sequence, wherein the longitudinal direction of the inlet portion 101, the neck portion 102, and the arched portion 103 The width of the section ( Figure 1b The vertical direction shown is the width direction of the gas ejector) first increases and then decreases, and the height ( Figure 1a The vertical direction shown is the height direction of the gas ejector) gradually decreasing.
[0027] In this way, from the inle...
PUM
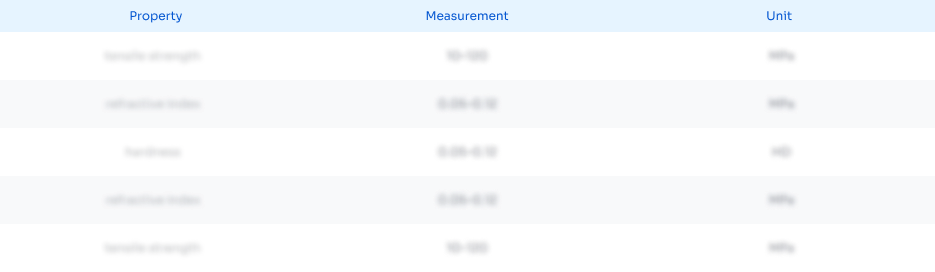
Abstract
Description
Claims
Application Information

- R&D
- Intellectual Property
- Life Sciences
- Materials
- Tech Scout
- Unparalleled Data Quality
- Higher Quality Content
- 60% Fewer Hallucinations
Browse by: Latest US Patents, China's latest patents, Technical Efficacy Thesaurus, Application Domain, Technology Topic, Popular Technical Reports.
© 2025 PatSnap. All rights reserved.Legal|Privacy policy|Modern Slavery Act Transparency Statement|Sitemap|About US| Contact US: help@patsnap.com