Exoskeleton robot shoulder joint design method based on four-connecting-rod mechanism
A technology of four-bar linkage mechanism and robot shoulder, which is applied in the direction of manipulators, program-controlled manipulators, joints, etc., can solve the problems of cost increase, affecting the wearer's comfort, the robot's range of motion, complex structure, etc., and achieve the effect of cost increase
- Summary
- Abstract
- Description
- Claims
- Application Information
AI Technical Summary
Problems solved by technology
Method used
Image
Examples
Embodiment Construction
[0029] specific implementation plan
[0030] The present invention will be further described in detail below through specific embodiments in conjunction with the accompanying drawings.
[0031] Because the frequency of the clavicle swinging back and forth is far less than that of the up and down swing, and the amplitude of the back and forth swing is also very small, the present invention ignores the clavicle swing back and forth and only considers the up and down swing. In other words, a set of power actuators will not be used to drive the parts of the exoskeleton to cooperate with the clavicle to swing back and forth.
[0032] The scheme of the present invention roughly divides following several steps:
[0033] The first step is to measure the length of the wearer's clavicle and humerus, and try to find the center point of the joint ball head as the endpoint.
[0034] In the second step, the wearer stands upright, with both arms hanging down naturally, and the humerus is v...
PUM
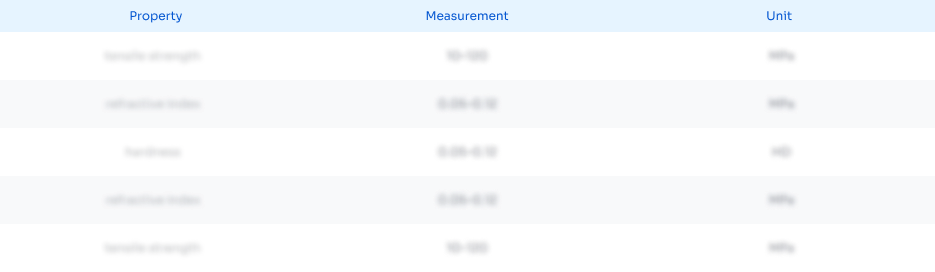
Abstract
Description
Claims
Application Information

- Generate Ideas
- Intellectual Property
- Life Sciences
- Materials
- Tech Scout
- Unparalleled Data Quality
- Higher Quality Content
- 60% Fewer Hallucinations
Browse by: Latest US Patents, China's latest patents, Technical Efficacy Thesaurus, Application Domain, Technology Topic, Popular Technical Reports.
© 2025 PatSnap. All rights reserved.Legal|Privacy policy|Modern Slavery Act Transparency Statement|Sitemap|About US| Contact US: help@patsnap.com