Method of compound welding twin arcs and cold wire pulse
A hybrid welding and double arc technology, applied in arc welding equipment, welding equipment, electrode accessories, etc., can solve problems such as weld defects and small welding parameters, increase the viscosity of the molten pool, reduce the probability of interference between the two arcs, and stabilize The effect of the welding process
- Summary
- Abstract
- Description
- Claims
- Application Information
AI Technical Summary
Problems solved by technology
Method used
Image
Examples
Embodiment approach
[0060] Implementation method: adopt the welding method of double arc and cold wire pulse hybrid welding, and implement the plate surfacing test. The specific implementation steps are as follows:
[0061] Basic steps of welding process:
[0062] (1) According to Figure 4 Connect equipment (including main system equipment and acquisition system equipment) at the position shown, and connect to a power supply with a power frequency of 50Hz;
[0063] (2) Adjust the working mode of the two PulseMIG-350, and adjust the pulse working mode of the two welding machines to one master and one slave through the front control panel, that is, the master welder guides the slave welder to send pulse signals;
[0064] (3) Adjust the preset current and voltage of the two welding machines, the preset current range: 80-220A, the preset voltage range: 18-32V;
[0065] (4) Adjust the corresponding pulse waveform input of the two welding machines, and the pulse waveform output that can be realized ...
PUM
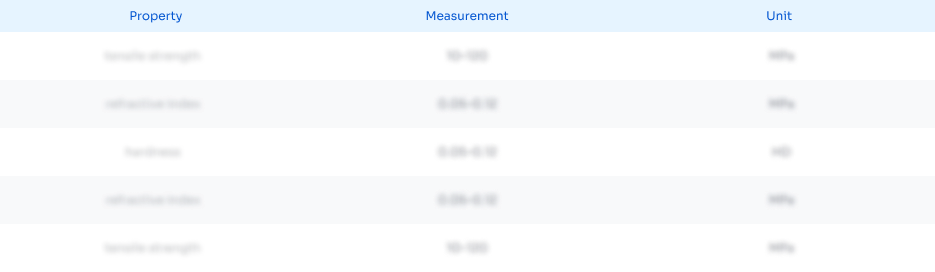
Abstract
Description
Claims
Application Information

- R&D Engineer
- R&D Manager
- IP Professional
- Industry Leading Data Capabilities
- Powerful AI technology
- Patent DNA Extraction
Browse by: Latest US Patents, China's latest patents, Technical Efficacy Thesaurus, Application Domain, Technology Topic, Popular Technical Reports.
© 2024 PatSnap. All rights reserved.Legal|Privacy policy|Modern Slavery Act Transparency Statement|Sitemap|About US| Contact US: help@patsnap.com