Damage Cycle Counting Method for Nonlinear Structural Parts and Its Fatigue Life Analysis Method
A technology of structural parts and counting method, applied in the field of non-linear structural parts damage cycle counting method and fatigue life analysis, can solve the problems of unpredictable fatigue life, limited use range of nonlinear structural parts, etc. The effect of high efficiency and high computational efficiency
- Summary
- Abstract
- Description
- Claims
- Application Information
AI Technical Summary
Problems solved by technology
Method used
Image
Examples
Embodiment 1
[0037] In this embodiment, damage cycle counting is performed on a rubber part under the action of two-axis load.
[0038] A method for counting damage cycles of rubber parts, including the following steps:
[0039] 1) Collect the two-axis random load received by the rubber part in use, and establish as figure 1 A two-axis random load spectrum is shown. The x-direction load and the y-direction load vary with time. If a rubber part is subjected to the two-axis random load, fatigue failure may occur. In order to calculate the load of the rubber component Life under the spectrum, the load spectrum needs to be decomposed;
[0040] 2 pairs figure 1 The load spectrum shown is sampled point by point, and the load at the same time is combined into the total load, which is marked as a load space vector containing direction and magnitude;
[0041] 3) Such as figure 2 As shown, the two-dimensional coordinate system is established, the load space vector in step 2) is merged into several directio...
Embodiment 2
[0049] A method for counting damage cycles of rubber parts, which is the same as Example 1, except that:
[0050] In step 3), a two-dimensional coordinate system is established, and the space coordinate system of the vector is divided at certain intervals. In this embodiment, the space is divided into 36 regions at 10 degree intervals, and the vectors falling on the regions are merged into the dividing line according to the principle of proximity In the above, the load spectrum is sampled point by point, and a series of points are obtained on the dividing line. The points on the same dividing line form a new unidirectional load spectrum according to time; for example, the point formed at the 0 degree dividing line The load spectrum in the direction of 0 degrees, the point of the 30-degree dividing line forms the load spectrum in the direction of 30 degrees; so far, a two-dimensional random load spectrum is split into the load spectrum in 18 directions (the positive and negative di...
PUM
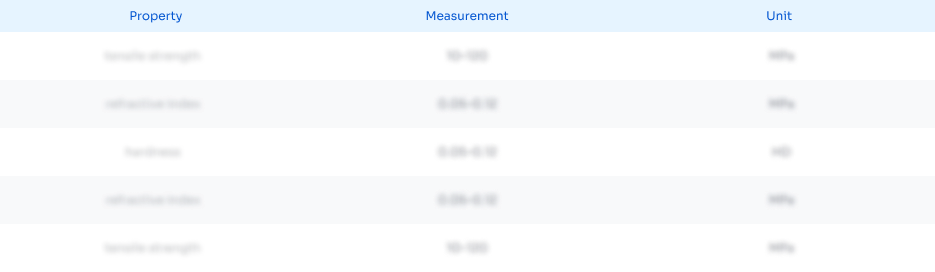
Abstract
Description
Claims
Application Information

- Generate Ideas
- Intellectual Property
- Life Sciences
- Materials
- Tech Scout
- Unparalleled Data Quality
- Higher Quality Content
- 60% Fewer Hallucinations
Browse by: Latest US Patents, China's latest patents, Technical Efficacy Thesaurus, Application Domain, Technology Topic, Popular Technical Reports.
© 2025 PatSnap. All rights reserved.Legal|Privacy policy|Modern Slavery Act Transparency Statement|Sitemap|About US| Contact US: help@patsnap.com