Steel rail contour real-time form identification and distortion calibration method based on three-layer matching
A calibration method and contour technology, applied in measuring devices, instruments, optical devices, etc., can solve the problems of decreased detection accuracy, acquisition of the longitudinal coordinates of the third-dimensional track, and difficulty in identifying other deformation contours in real time, so as to ensure real-time performance. Effect
- Summary
- Abstract
- Description
- Claims
- Application Information
AI Technical Summary
Problems solved by technology
Method used
Image
Examples
Embodiment Construction
[0048] According to the characteristics of affine transformation between the measured deformation profile and the unworn area of the standard template profile under the influence of vibration, the present invention proposes a method based on rail jaw point, rail The real-time shape recognition and distortion calibration method of the rail profile with the three-layer matching of the head straight line area and the rail waist feature area, and the most widely used 60Kg / m rail in my country has carried out deformation profile recognition and calibration experiments under the influence of various vibrations, and achieved Good experimental results.
[0049] The method includes three steps: collecting and counting contour matching feature points and classification thresholds for subsequent recognition and calibration; real-time shape recognition of random measurement contours; and calibration of deformed contours. The overall process is as Figure 4 shown.
[0050] 1. Acquisition...
PUM
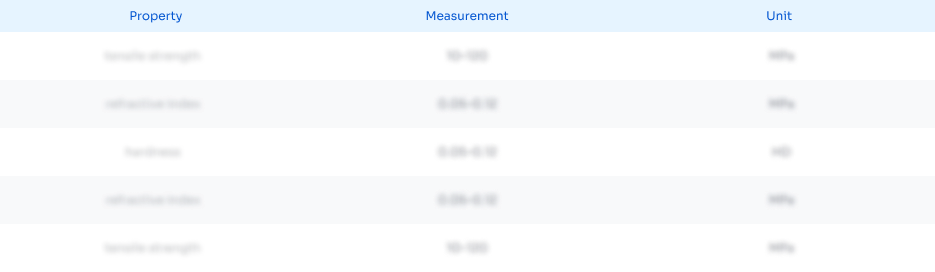
Abstract
Description
Claims
Application Information

- Generate Ideas
- Intellectual Property
- Life Sciences
- Materials
- Tech Scout
- Unparalleled Data Quality
- Higher Quality Content
- 60% Fewer Hallucinations
Browse by: Latest US Patents, China's latest patents, Technical Efficacy Thesaurus, Application Domain, Technology Topic, Popular Technical Reports.
© 2025 PatSnap. All rights reserved.Legal|Privacy policy|Modern Slavery Act Transparency Statement|Sitemap|About US| Contact US: help@patsnap.com