Annealing process for comb teeth of turbonator
A technology of steam turbine generator and annealing process, which is applied in the field of comb tooth annealing process of steam turbine generator, which can solve the problems that the design requirements of comb teeth cannot be guaranteed, the strength and hardness decrease, and the heating of materials is not uniform, so as to achieve the guaranteed strength And hardness requirements, accurate annealing temperature, uniform heating effect
- Summary
- Abstract
- Description
- Claims
- Application Information
AI Technical Summary
Problems solved by technology
Method used
Examples
Embodiment Construction
[0016] A kind of steam turbine generator comb tooth annealing process, its process steps are as follows:
[0017] 1) Cutting material: H70-Y2 semi-hard copper plate is selected as the comb material, the thickness is 2mm, and the length is according to the requirements of the drawing;
[0018] 2) Furnace loading: use a well-type resistance furnace with a fan for annealing, put the combs vertically into the heat treatment hoisting tool basket after unloading, put the furnace temperature below 150°C into the furnace, and hoist the tool basket into the heat treatment furnace;
[0019] 3) Annealing: the comb teeth are heated to 420°C±10°C with the furnace, and then kept for 1 hour, then taken out of the furnace and cooled to room temperature in the air;
[0020] 4) Machining: After annealing, it is processed into the size required by the drawing;
[0021] 5) Bending: The comb teeth are bent on a special bending tool.
[0022] By completing the above process content, the heat trea...
PUM
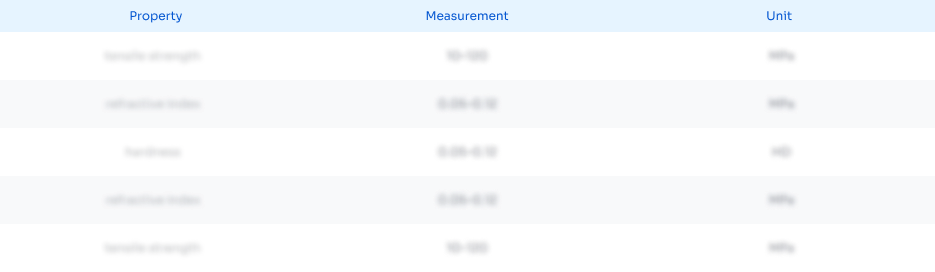
Abstract
Description
Claims
Application Information

- Generate Ideas
- Intellectual Property
- Life Sciences
- Materials
- Tech Scout
- Unparalleled Data Quality
- Higher Quality Content
- 60% Fewer Hallucinations
Browse by: Latest US Patents, China's latest patents, Technical Efficacy Thesaurus, Application Domain, Technology Topic, Popular Technical Reports.
© 2025 PatSnap. All rights reserved.Legal|Privacy policy|Modern Slavery Act Transparency Statement|Sitemap|About US| Contact US: help@patsnap.com