Method for leaching extracted vanadium from vanadium-containing raw material roasted clinker through ammonium oxalate
A technology for roasting clinker and ammonium oxalate, applied in the field of vanadium chemical industry and metallurgy, can solve the problems of short process flow, poor operating environment, loss of leaching agent, etc., and achieve the effects of short process flow, low production cost and less impurity content
- Summary
- Abstract
- Description
- Claims
- Application Information
AI Technical Summary
Problems solved by technology
Method used
Examples
Embodiment 1
[0034] will V 2 o 5 Vanadium slag with a content of 10.5% according to CaO / V 2 o 5 The molar ratio is 2, and the clinker obtained after calcification and roasting at 600°C for 4 hours is leached to extract vanadium in ammonium oxalate solution. The leaching temperature is 30°C, the leaching liquid-solid ratio is 10mL / g, and the leaching time is 2h. Tailings and vanadium-containing leachate. Wherein, the NH in the ammonium oxalate solution 4 + The mass concentration is 100g / L, C 2 o 4 2- The mass concentration is 400g / L; The ammonium oxalate solution is obtained by directly dissolving ammonium oxalate solid in a solvent.
[0035] The leached slag was washed, dried, weighed and analyzed for the vanadium content of the residue. It was tested that the vanadium transfer leaching rate was 91%.
Embodiment 2
[0037] will V 2 o 5 Vanadium slag with a content of 14.7% according to CaO / V 2 o 5 The molar ratio is 2.5, and the clinker ammonium oxalate solution obtained by calcification and roasting at 700°C for 5 hours is leached to extract vanadium. The leaching temperature is 75°C, the leaching liquid-solid ratio is 5mL / g, and the leaching time is 1h. vanadium-containing leachate. Wherein, the NH in the ammonium oxalate solution 4 + The mass concentration is 200g / L, C 2 o 4 2- The mass concentration is 200g / L; the ammonium oxalate solution is obtained by directly dissolving ammonium oxalate solid in a solvent.
[0038] The leached slag was washed, dried, weighed and analyzed for the vanadium content of the residue. It was tested that the vanadium transfer leaching rate was 90%.
Embodiment 3
[0040] will V 2 o 5 Vanadium slag with 20% content according to CaO / V 2 o 5 The molar ratio is 3, and the clinker obtained after calcification and roasting at 1000°C for 0.5h is leached to extract vanadium in ammonium oxalate solution. The leaching temperature is 20°C, the leaching liquid-solid ratio is 20mL / g, and the leaching time is 6h. Tailings and vanadium-containing leachate. Wherein, the NH in the ammonium oxalate solution 4 + The mass concentration is 150g / L, C 2 o 4 2- The mass concentration is 200g / L; the ammonium oxalate solution is obtained by directly dissolving ammonium oxalate solid in a solvent.
[0041] The leached slag was washed, dried, weighed and analyzed for the vanadium content of the residue. It was tested that the vanadium transfer leaching rate was 93%.
PUM
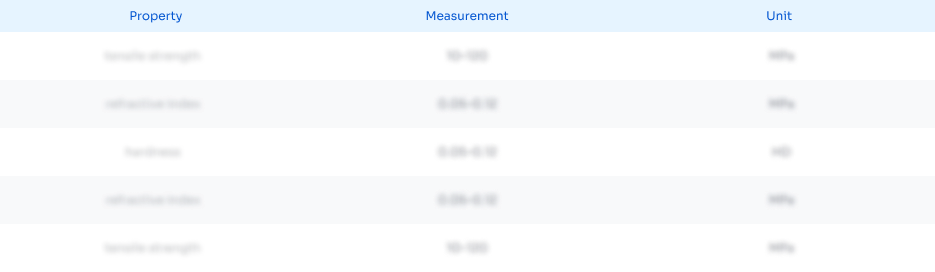
Abstract
Description
Claims
Application Information

- Generate Ideas
- Intellectual Property
- Life Sciences
- Materials
- Tech Scout
- Unparalleled Data Quality
- Higher Quality Content
- 60% Fewer Hallucinations
Browse by: Latest US Patents, China's latest patents, Technical Efficacy Thesaurus, Application Domain, Technology Topic, Popular Technical Reports.
© 2025 PatSnap. All rights reserved.Legal|Privacy policy|Modern Slavery Act Transparency Statement|Sitemap|About US| Contact US: help@patsnap.com