Pneumatic pipeline robot system based on pneumatic tendon
A robot system and pneumatic pipeline technology, applied in the field of robots, can solve the problems of self-weight, small step distance, complex structure, etc., and achieve the effect of easy operation, simple structure and simplified mechanism
- Summary
- Abstract
- Description
- Claims
- Application Information
AI Technical Summary
Problems solved by technology
Method used
Image
Examples
Embodiment Construction
[0038] see Image 6 , the present invention is based on the pneumatic muscle pneumatic pipeline robot system, which includes a support module 1, a telescopic module, and a support module 2 connected in sequence. , the joint bearing is a spherical bearing 604 . The spherical pair in the spherical bearing enables the two support modules to orbit a space angle θ relative to the telescopic module, so the robot has the ability to bend.
[0039] In this embodiment, the support module 1 and the support module 2 are respectively provided with two support cylinders 602 and four guide wheels 601, and the four guide wheels 601 are distributed in pairs before and after the support cylinder 602, so that the movement is more stable when driving forward . The end of the support cylinder 602 is provided with a support block 603 . It is more stable to support by supporting the cylinder to drive the support block.
[0040] see Figure 7 The difference between the second embodiment and the ...
PUM
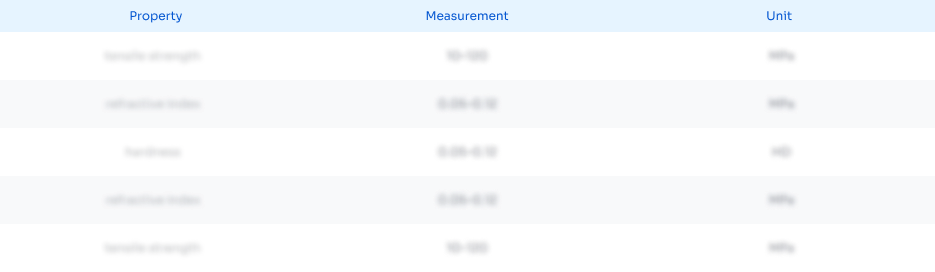
Abstract
Description
Claims
Application Information

- R&D
- Intellectual Property
- Life Sciences
- Materials
- Tech Scout
- Unparalleled Data Quality
- Higher Quality Content
- 60% Fewer Hallucinations
Browse by: Latest US Patents, China's latest patents, Technical Efficacy Thesaurus, Application Domain, Technology Topic, Popular Technical Reports.
© 2025 PatSnap. All rights reserved.Legal|Privacy policy|Modern Slavery Act Transparency Statement|Sitemap|About US| Contact US: help@patsnap.com