Composite reverse osmosis membrane with high salt removing rate and controllable flux and method for preparing composite reverse osmosis membrane
A reverse osmosis membrane, composite technology, applied in reverse osmosis, semi-permeable membrane separation, chemical instruments and methods, etc., can solve the problems of difficult membrane desalination and flux control, low water production, and high working pressure.
- Summary
- Abstract
- Description
- Claims
- Application Information
AI Technical Summary
Problems solved by technology
Method used
Image
Examples
Embodiment 1
[0025] The reverse osmosis membrane production method is as follows:
[0026] 1. Preparation of aqueous phase solution: Add 3kg of m-phenylenediamine, 0.5kg of sodium dodecylbenzenesulfonate, and 4kg of N-methylpyrrolidone to 92.5kg of water, and stir to obtain an aqueous phase solution;
[0027] 2. Preparation of oil phase solution: Dissolve 0.1 kg of trimesoyl chloride in 100 kg of naphtha, stir well to obtain oil phase solution;
[0028] 3. First, coat the water-phase solution on the bottom membrane of the polysulfone support layer. After removing the excess solution on the surface with a low-pressure air knife, let the bottom membrane adsorbed with the water-phase solution pass through a closed space with a heating and ventilation system to control The internal temperature is 26°C, the relative humidity is 60%, and the time is 1min, so that the moisture on the surface of the bottom film is further volatilized. Keep it in an oven at ℃ for 5 minutes, dry the oil phase liqui...
Embodiment 2
[0031] The reverse osmosis membrane production method is as follows:
[0032] 1. Preparation of aqueous phase solution: Add 3kg of m-phenylenediamine, 0.5kg of sodium dodecylbenzenesulfonate, and 4kg of dimethyl sulfoxide to 92.5kg of water, and stir to obtain an aqueous phase solution;
[0033] 2, the preparation of oil phase solution: with embodiment 1;
[0034] 3. The film making method is the same as in Example 1.
[0035] The membrane detection method is the same as in Example 1, and the results are shown in Table 1.
Embodiment 3
[0037] The reverse osmosis membrane production method is as follows:
[0038] 1. Preparation of aqueous phase solution: Add 3kg m-phenylenediamine, 0.5kg sodium dodecylbenzenesulfonate, 3kg N-methylpyrrolidone, 1kg dimethyl sulfoxide to 92.5kg water, stir well to obtain aqueous phase solution ;
[0039] 2, the preparation of oil phase solution: with embodiment 1;
[0040] 3. The film making method is the same as in Example 1.
[0041] The membrane detection method is the same as in Example 1, and the results are shown in Table 1.
PUM
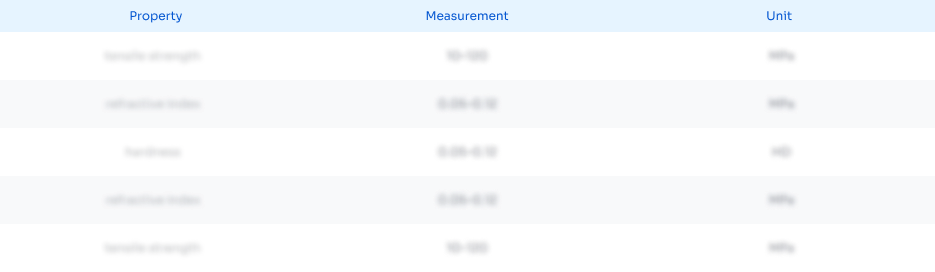
Abstract
Description
Claims
Application Information

- Generate Ideas
- Intellectual Property
- Life Sciences
- Materials
- Tech Scout
- Unparalleled Data Quality
- Higher Quality Content
- 60% Fewer Hallucinations
Browse by: Latest US Patents, China's latest patents, Technical Efficacy Thesaurus, Application Domain, Technology Topic, Popular Technical Reports.
© 2025 PatSnap. All rights reserved.Legal|Privacy policy|Modern Slavery Act Transparency Statement|Sitemap|About US| Contact US: help@patsnap.com