Glass tube cladding extrusion molding process
An extrusion process and glass tube technology, which is applied in the production field of glass tube coating, can solve the problems of incapable of mass production, complex assembly process, easy to turn yellow, etc., to simplify the assembly process, reduce production costs, and improve production efficiency. Effect
- Summary
- Abstract
- Description
- Claims
- Application Information
AI Technical Summary
Benefits of technology
Problems solved by technology
Method used
Image
Examples
Embodiment
[0025] Example: see figure 1 , a glass tube-coated extrusion molding process of the present invention, comprising a feeding traction device 1, an extruder 2, a cooling device 3, a traction device 4, an automatic cutting device 5 and an automatic receiving device 6, and the glass tube 7 is drawn by feeding The device 1 enters the extruder 2, and through the extruder 2, the outer wall of the glass tube 7 is covered with a layer of glue to form a wrapped glass tube 8, and the wrapped glass tube 8 enters the cooling device 3 for cooling, and after being drawn The device 4 continuously wraps the glass tube 8 into the automatic cutting device 5 , and finally wraps the glass tube 8 through the automatic receiving device 6 .
[0026] The extrusion molding process of described glass tube coating is:
[0027] The glass tube 7 is extruded into the extruded part 2 through the feeding traction device 1;
[0028] The wrapped glass tube 8 coated with the rubber layer enters the cooling dev...
PUM
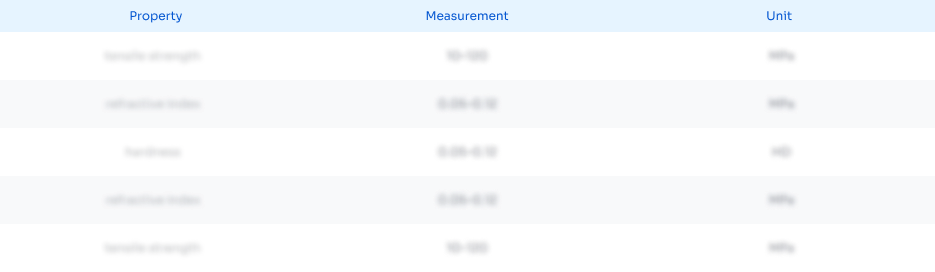
Abstract
Description
Claims
Application Information

- R&D
- Intellectual Property
- Life Sciences
- Materials
- Tech Scout
- Unparalleled Data Quality
- Higher Quality Content
- 60% Fewer Hallucinations
Browse by: Latest US Patents, China's latest patents, Technical Efficacy Thesaurus, Application Domain, Technology Topic, Popular Technical Reports.
© 2025 PatSnap. All rights reserved.Legal|Privacy policy|Modern Slavery Act Transparency Statement|Sitemap|About US| Contact US: help@patsnap.com