A spraying process of release agent in banburying workshop
A release agent and workshop technology, applied in coatings, spray booths, spraying devices, etc., can solve the problems of high viscosity of mixing adhesives, difficulties in processing and transportation, mutual adhesion, etc., achieve low single-layer rate, improve efficiency, Avoid the effect of reunion
- Summary
- Abstract
- Description
- Claims
- Application Information
AI Technical Summary
Problems solved by technology
Method used
Image
Examples
Embodiment 1
[0040] Embodiment 1: a kind of spraying process that adopts the auxiliary machine system under the internal mixer of the present invention to carry out the release agent, specifically comprises the following steps:
[0041] (1) Dissolving graphene oxide in water to obtain a graphene oxide aqueous solution, the mass percent concentration of the graphene oxide aqueous solution is 2‰, and the graphene oxide aqueous solution remains neutral;
[0042] (2) After the compounded rubber is pressed by the tablet press, the temperature of the mixed rubber is 90°C, and it is sent to the cooling pool by the conveying device. The water temperature of the cooling pool is kept below 60°C; During the process, the fan is blown dry, and with the evaporation of water, the mixed rubber material continues to cool down; in the above process, the temperature of the water in the cooling pool should be closely monitored. If the water temperature is too high, it is necessary to replace the water in the c...
Embodiment 2
[0044] Embodiment 2: a kind of spraying process that adopts the auxiliary machine system under the internal mixer of the present invention to carry out the release agent, specifically comprises the following steps:
[0045] (1) Dissolving graphene oxide in water to obtain a graphene oxide aqueous solution, the mass percent concentration of the graphene oxide aqueous solution is 3‰, and the graphene oxide aqueous solution remains neutral;
[0046] (2) After the compounded rubber is pressed by the tablet press, the temperature of the mixed rubber is 160°C, and it is sent to the cooling pool by the conveying device, and the water temperature of the cooling pool is kept below 60°C; after cooling in the cooling pool, it is transferred During the process, the fan is blown dry, and with the evaporation of water, the mixed rubber material continues to cool down; in the above process, the temperature of the water in the cooling pool should be closely monitored. If the water temperature ...
Embodiment 3
[0048] Embodiment 3: a kind of spraying process that adopts the auxiliary machine system under the internal mixer of the present invention to carry out the release agent, specifically comprises the following steps:
[0049] (1) Dissolving graphene oxide in water to obtain a graphene oxide aqueous solution, the mass percent concentration of the graphene oxide aqueous solution is 2.5‰, and the graphene oxide aqueous solution remains neutral;
[0050] (2) After the compounded rubber is pressed by the tablet press, the temperature of the mixed rubber is 100°C, and it is sent to the cooling pool by the conveying device, and the water temperature of the cooling pool is maintained below 60°C; after cooling in the cooling pool, it is transferred During the process, the fan is blown dry, and with the evaporation of water, the mixed rubber material continues to cool down; in the above process, the temperature of the water in the cooling pool should be closely monitored. If the water temp...
PUM
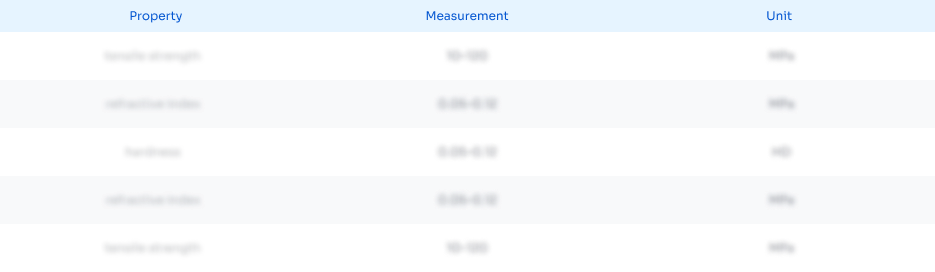
Abstract
Description
Claims
Application Information

- R&D
- Intellectual Property
- Life Sciences
- Materials
- Tech Scout
- Unparalleled Data Quality
- Higher Quality Content
- 60% Fewer Hallucinations
Browse by: Latest US Patents, China's latest patents, Technical Efficacy Thesaurus, Application Domain, Technology Topic, Popular Technical Reports.
© 2025 PatSnap. All rights reserved.Legal|Privacy policy|Modern Slavery Act Transparency Statement|Sitemap|About US| Contact US: help@patsnap.com