Combined drill molding milling cutter and manufacturing method thereof
A technology for forming milling cutters and manufacturing methods, applied in milling cutters, manufacturing tools, drilling and other directions, can solve problems such as size mismatch, and achieve the effect of simplifying processing procedures, reducing the risk of rework or scrapping, and having high precision
- Summary
- Abstract
- Description
- Claims
- Application Information
AI Technical Summary
Problems solved by technology
Method used
Image
Examples
Embodiment 1
[0036] Please refer to figure 1 , figure 1 It is a structural schematic diagram of a composite drill forming milling cutter disclosed in an embodiment of the present invention. Such as figure 1 As shown, the compound drill form milling cutter can include:
[0037]The shank 1 and the drill body 2, wherein the shank 1 and the drill body 2 are cylindrical structures, the diameter of the shank 1 is larger than the diameter of the drill body 2, and the lower end of the shank 1 is coaxially connected with the upper end of the drill body 2, The lower end of the drill body 2 is coaxially connected with the upper end of the transition section 3 of the cylindrical structure, and the diameter of the transition section 3 is smaller than the diameter of the drill body 2; The other water end surface of the table 4 is coaxially connected with the upper end of the drill section 5 of the cylindrical structure, and the lower end of the drill section 5 shrinks into a drill structure 51; The ...
Embodiment 2
[0049] Please refer to image 3 , image 3 It is a schematic flowchart of a manufacturing method of a compound drill forming milling cutter disclosed in an embodiment of the present invention. Such as image 3 Shown, the manufacture method of this compound drill form milling cutter can comprise the following steps:
[0050] 301. Select the shank and the drill body, wherein both the shank and the drill body are cylindrical structures, and the diameter of the shank is larger than the diameter of the drill body;
[0051] 302. Select the transition section, the truncated cone and the drill section, wherein the transition section and the drill section are cylindrical structures, and the diameter of the transition section is smaller than the diameter of the drill body; the lower end of the drill section shrinks into a drill structure; the diameter of the drill section is as The diameter of the processed flange rivet hole, the angle between the side of the truncated cone and the c...
PUM
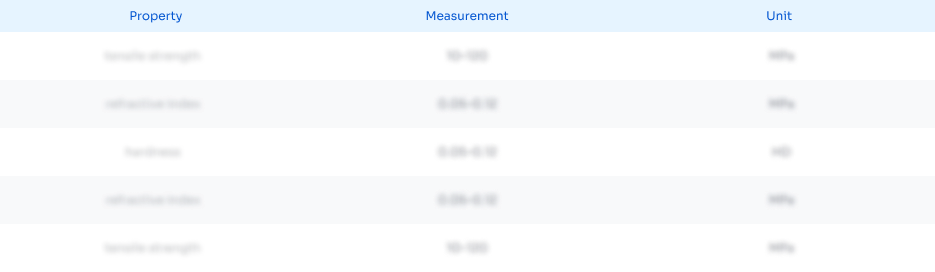
Abstract
Description
Claims
Application Information

- R&D Engineer
- R&D Manager
- IP Professional
- Industry Leading Data Capabilities
- Powerful AI technology
- Patent DNA Extraction
Browse by: Latest US Patents, China's latest patents, Technical Efficacy Thesaurus, Application Domain, Technology Topic, Popular Technical Reports.
© 2024 PatSnap. All rights reserved.Legal|Privacy policy|Modern Slavery Act Transparency Statement|Sitemap|About US| Contact US: help@patsnap.com