Sensorless rotor position identification system and method for brushless direct current motor
A technology of brushing DC motor and rotor position, applied in control system, electronic commutator, electronic commutation motor control and other directions, can solve the problems of reducing the reliability of the control system, increasing the cost, increasing the complexity of the motor structure, etc.
- Summary
- Abstract
- Description
- Claims
- Application Information
AI Technical Summary
Problems solved by technology
Method used
Image
Examples
Embodiment Construction
[0038] Further illustrate the present invention below in conjunction with accompanying drawing. like Figure 1-9 Shown, concrete method of the present invention is as follows:
[0039] like figure 1Shown is a system structure block diagram of the present invention, the system includes 220V AC power supply 1, single-phase uncontrollable rectifier bridge module 2, filter capacitor group 3, bus voltage sensor 4, three-phase inverter bridge module 5, current closed-loop regulation Unit 6, DSP control system 7, power management circuit 8, current sensor 12, position detection circuit 13 and brushless DC motor 14; 220V AC power supply 1 is rectified by single-phase uncontrollable rectifier bridge module 2 to obtain DC voltage input three-phase The inverter bridge module 5; the DSP control system 7 captures the commutation signal 11 generated by the position detection circuit 13 according to the ECAP module 10 and passes through the current closed-loop adjustment unit 6, and then ...
PUM
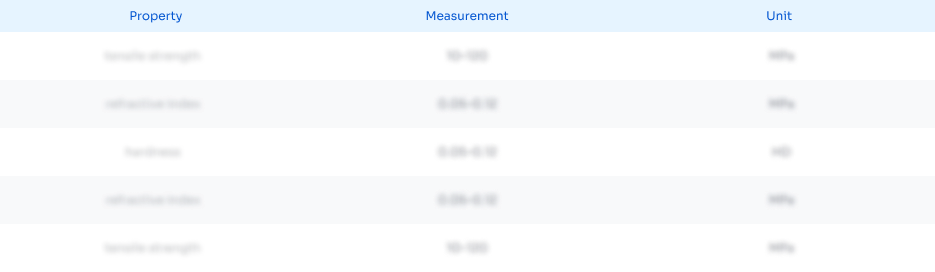
Abstract
Description
Claims
Application Information

- R&D Engineer
- R&D Manager
- IP Professional
- Industry Leading Data Capabilities
- Powerful AI technology
- Patent DNA Extraction
Browse by: Latest US Patents, China's latest patents, Technical Efficacy Thesaurus, Application Domain, Technology Topic, Popular Technical Reports.
© 2024 PatSnap. All rights reserved.Legal|Privacy policy|Modern Slavery Act Transparency Statement|Sitemap|About US| Contact US: help@patsnap.com