Underwater camera calibration method
A camera calibration, camera technology, applied in image analysis, image enhancement, instruments and other directions, can solve the problem that the calibration accuracy cannot meet the high-precision measurement, it is regarded as a linear change, and it is difficult to achieve.
- Summary
- Abstract
- Description
- Claims
- Application Information
AI Technical Summary
Problems solved by technology
Method used
Image
Examples
Embodiment Construction
[0037] The present invention will be further described below in conjunction with the accompanying drawings.
[0038] A high-precision underwater camera calibration method. When the underwater camera system is imaging, the light rays mathematically model the physical process of underwater imaging in the order of water-diaphragm-air-camera lens. The difference between air and water camera parameters is that the imaging model in air cannot be applied in water due to the existence of the refraction plane, and the imaging model of the underwater camera needs to be modeled.
[0039] The incident light is refracted twice at the water-proof plane, but the refraction does not change the angle contrast between water and air, and because the water-proof shell is made very thin, the refraction in the water-proof shell has a great impact on the entire refraction. process is negligible, so the process of refraction imaging is as figure 1 shown.
[0040] Assuming that the surface of the w...
PUM
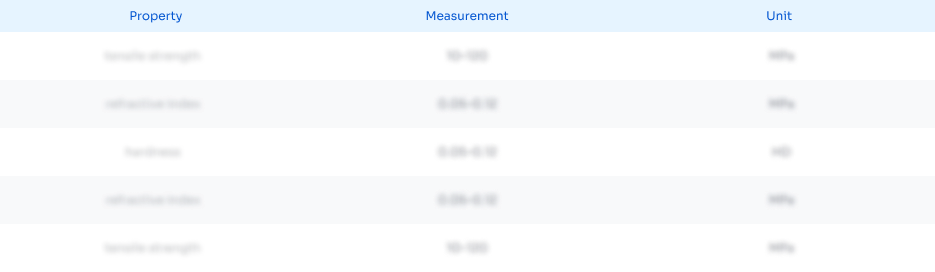
Abstract
Description
Claims
Application Information

- Generate Ideas
- Intellectual Property
- Life Sciences
- Materials
- Tech Scout
- Unparalleled Data Quality
- Higher Quality Content
- 60% Fewer Hallucinations
Browse by: Latest US Patents, China's latest patents, Technical Efficacy Thesaurus, Application Domain, Technology Topic, Popular Technical Reports.
© 2025 PatSnap. All rights reserved.Legal|Privacy policy|Modern Slavery Act Transparency Statement|Sitemap|About US| Contact US: help@patsnap.com