Non-contact angle sensor for heavy duty machinery and angle correction method
An angle sensor, non-contact technology, applied in the direction of instruments, using electrical devices, using electromagnetic means, etc., can solve the problems of anti-interference, poor anti-vibration performance, inability to obtain accurate angle values, and low service life of the sensor. Convenience, high reliability and long service life
- Summary
- Abstract
- Description
- Claims
- Application Information
AI Technical Summary
Problems solved by technology
Method used
Image
Examples
Embodiment Construction
[0011] Examples, see attached figure 1 , The sensor housing 6 of the non-contact angle sensor for heavy-duty machinery is made of copper, which can effectively avoid electromagnetic interference around the sensor. A groove is arranged at the bottom of the upper inner cavity of the sensor housing 6 , and an isolation ring 17 is installed in the groove, and a circuit board 13 is installed in the sensor inner cavity above the isolation ring 17 . Connecting shaft 12 is housed with bearing 9 in the lower inner cavity of sensor housing 6, is provided with magnetite mounting groove 12-1 at the top center of connecting shaft 12, and magnetite 7 is housed in magnetizing mounting groove 12-1. A sensor chip 16 is connected to the circuit board 13 facing the magnet 7 , and an acceleration sensor 15 and a gyroscope module 14 are connected to the upper middle of the circuit board 13 . A rubber covering layer 11 is sealed between the inner bottom of the sensor housing 6 and the outer circum...
PUM
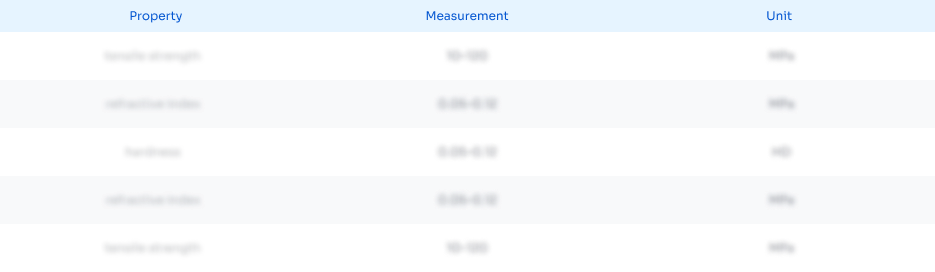
Abstract
Description
Claims
Application Information

- R&D Engineer
- R&D Manager
- IP Professional
- Industry Leading Data Capabilities
- Powerful AI technology
- Patent DNA Extraction
Browse by: Latest US Patents, China's latest patents, Technical Efficacy Thesaurus, Application Domain, Technology Topic, Popular Technical Reports.
© 2024 PatSnap. All rights reserved.Legal|Privacy policy|Modern Slavery Act Transparency Statement|Sitemap|About US| Contact US: help@patsnap.com