Coking coal blending method with participation of lean coking coal
A technology for lean coking coal and coking coal is applied in the field of coking coal blending with lean coking coal. Cost coal blending, easy to achieve, good quality effect
- Summary
- Abstract
- Description
- Claims
- Application Information
AI Technical Summary
Problems solved by technology
Method used
Image
Examples
Embodiment 1
[0024] Coking coal components and weight percentages are:
[0025] 1 / 3 coking coal: 16%;
[0026] Dry ash-free base volatile content 32%≤V daf ≤34% fat coal: 10%;
[0027] Dry ash-free base volatile content 28%≤V daf <32% fat coal: 10%;
[0028] Caking index G≥78 coking coal: 34%;
[0029] Caking index 75≤G<78 Coking coal: 10%;
[0030] Lean coking coal: 20%.
[0031] Lean coking coal quality index: ash content: 9.1%, volatile matter: 19.64%, G value: 72, Y value: 6.5mm.
[0032] Coal quality index of coking coal: ash content A d : 8.34%, Sulfur S td : 0.63%, Ash V daf : 26.38%.
[0033] The distribution results of vitrinite reflectance of coking coal are shown in Table 1.
[0034] Table 1 Example 1 coking coal vitrinite reflectance distribution results (%)
[0035]
[0036] The quality of coke obtained in a coke oven above 6 meters: coke crushing strength M 40 : 89.38%; coke strength CSR after reaction: 63.60%; ash A d : 11.61%; Sulfur S td : 0.60%.
Embodiment 2
[0038] Coking coal composition and weight percentage:
[0039] 1 / 3 coking coal: 10%;
[0040] Dry ash-free base volatile content 32%≤V daf ≤34% fat coal: 16%;
[0041] Dry ash-free base volatile content 28%≤V daf <32% fat coal: 8%;
[0042] Caking index G≥78 coking coal 1 # : 30%;
[0043] Caking index G≥78 coking coal 2 # : 12%;
[0044] Caking index 75≤G<78 Coking coal: 0%;
[0045] Lean coking coal: 24%.
[0046] Lean coking coal quality index: ash content: 9.2%, volatile matter: 19.18%, G value: 64.3, Y value: 9.3mm.
[0047] Coking coal quality index: ash A d : 9.30%, Sulfur S td : 0.90%, gray hair content V daf : 26.51%.
[0048] The distribution results of vitrinite reflectance of coking coal are shown in Table 2.
[0049] Table 2 Example 2 coking coal vitrinite reflectance distribution results (%)
[0050]
[0051] The quality of coke obtained in a coke oven above 6 meters: coke crushing strength M 40 : 89.47%; coke strength CSR after reaction: 65.18...
Embodiment 3
[0053] Coking coal composition and weight percentage:
[0054] 1 / 3 coking coal: 8%;
[0055] Dry ash-free base volatile content 32%≤V daf ≤34% fat coal: 16%;
[0056] Dry ash-free base volatile content 28%≤V daf <32% fat coal: 8%;
[0057] Caking index G≥78 coking coal 1 # : 34%;
[0058] Caking index G≥78 coking coal 2 # : 12%;
[0059] Caking index 75≤G<78 Coking coal: 0%;
[0060] Lean coking coal: 22%.
[0061] Lean coking coal quality index: ash content: 11.29%, volatile matter: 18.70%, G value: 74, Y value: 7.5mm.
[0062] Coal quality index of mixed coal: ash content A d : 9.29%; Sulfur S td : 0.90%; gray hair component V daf : 26.34%.
[0063] The distribution results of vitrinite reflectance of coking coal are shown in Table 3.
[0064] Table 3 Example 3 coking coal vitrinite reflectance distribution results (%)
[0065]
[0066]The quality of coke obtained in a coke oven above 6 meters: coke crushing strength M 40 : 87.30%; coke strength CSR after ...
PUM
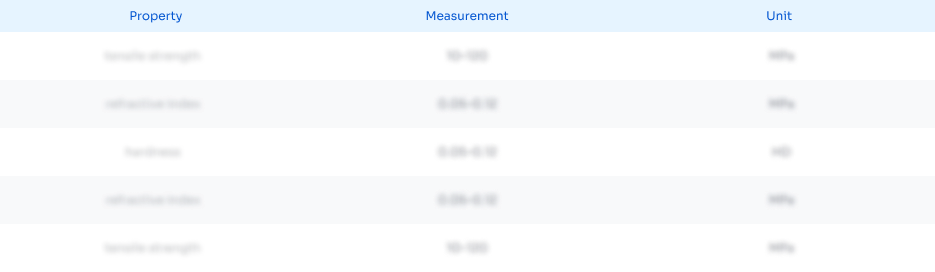
Abstract
Description
Claims
Application Information

- Generate Ideas
- Intellectual Property
- Life Sciences
- Materials
- Tech Scout
- Unparalleled Data Quality
- Higher Quality Content
- 60% Fewer Hallucinations
Browse by: Latest US Patents, China's latest patents, Technical Efficacy Thesaurus, Application Domain, Technology Topic, Popular Technical Reports.
© 2025 PatSnap. All rights reserved.Legal|Privacy policy|Modern Slavery Act Transparency Statement|Sitemap|About US| Contact US: help@patsnap.com